
Los aditivos son las sustancias añadidas en peso/volumen inferior al 5% de la masa y que actúan sobre la matriz cementicia para dotarla de características diversas.
Los aditivos los definía Prof. Dr. Don José Calleja Carrete, asesor de IECA, como “aquellas sustancias que añadidas al conglomerante (pasta, mortero u hormigón) en el momento de su elaboración, en las condiciones adecuadas, en la forma conveniente y en las dosis precisas, tienen por finalidad modificar en sentido positivo y con carácter permanente las propiedades del conglomerado, o en su caso conferírselas, para su mejor comportamiento en todos o en algún aspecto, tanto en estado fresco como una vez fraguado y endurecido».
La definición es amplia y deja claro que los aditivos tienen que modificar en sentido positivo, es decir: «que la mejora ha de ser permanente y tanto en estado fresco como endurecido, esto es, su acción ha de ser estable a lo largo del tiempo».
Los aditivos tienen una «función principal» que determina la utilización del aditivo y que se caracteriza por producir una modificación determinada, y solamente una, de alguna de las características del hormigón-concreto, mortero o pasta, pudiendo tener, además, una «función secundaria» y accesoria de modificar alguna o algunas de las características de estos materiales, independientemente de la que defina la función principal. A estas funciones se las podría denominar también «indicaciones».
Es normal que un aditivo produzca modificaciones inevitables de ciertas propiedades de los hormigones-concretos, que no se requieran como función secundaria y que, por tanto, no son deseadas. A esta propiedad del aditivo se denomina «efecto secundario» o «contraindicación».
El efecto de un mismo aditivo, dosificado en la misma proporción, puede ser diferente de acuerdo con el tipo de cemento y/o agregados con el que se esté utilizando; así, aditivos muy eficaces con cementos portland, lo son menos con puzolánicos y con los siderúrgicos. También encontramos aditivos muy enérgicos con áridos calizos que al utilizarse con áridos silíceos o graníticos pierden eficacia, es todo cuestión de método empírico: prueba-error… ensaye y constate usted mismo.
La dosis para emplear de aditivo en el hormigón.concreto es muy importante, pues, no hay que esperar que, a doble dosis corresponda doble efecto ni a mitad de dosis mitad de acción.
Con determinados aditivos, puede darse, además, el caso de que el sobrepasar ciertas dosis sea muy contraproducente para el hormigón-concreto o que incluso se consigan efectos contrarios a los deseados.
El correcto empleo de un aditivo supone no solo que se haya elegido correctamente para el empeño que se pretende, sino que esté, además, bien dosificado y aprovechado eficazmente en la medida de lo posible.
Actualmente el empleo de los aditivos en los morteros y hormigones-concretos ha experimentado un gran incremento como consecuencia de la mejor calidad de estos. Puede decirse que, un tanto por ciento muy elevado del hormigón que se fabrica lleva incorporado un tipo u otro de aditivo y que, si estos son de calidad y están correctamente empleados, permiten conseguir hormigones-concretos dóciles, resistentes, durables y económicos.
En el caso de los hormigones-concretos de pavimentos al tener que ser trabajados en su fase gel tengamos en cuenta que el conocimiento de los aditivos y sus efectos en los distintos tipos de hormigón se vuelve crucial para facilitar la puesta en obra, la trabajabilidad, la velocidad de fraguado, el cambio de volumen y la durabilidad final.
Es importante tener en cuenta que para ejecutar un pavimento de hormigón-concreto se requieren un/os aditivos diferentes a los aditivos comunes para hormigones comunes.
El artículo 31.2 de Capítulo 8 del Código Técnico Estructural español y en el Capítulo 5.15 del Eurocódigo 2 UNE EN-206-1, se recoge, seis clases de aditivos de acuerdo con la norma UNE-EN 934-2, que los certifica y que los clasifica por su función principal, empleados en los hormigones-concretos, morteros o pastas en clases específicas y entre las más comunes se encuentran. Las tablas que siguen a continuación definen los mismo.
1.CLASES DE ADITIVOS QUE PUEDEN UTILIZARSE EN LA CONFECCIÓN DE HORMIGONES-CONCRETOS PARA PAVIMENTOS

🡪Modificaciones de la reología en estado fresco | ||||||
Tipo | Características | Idoneidad para uso en hormigones de pavimentos | ||||
Fluidificantes/ Reductores de agua. | *Aumentan la trabajabilidad para un mismo contenido de agua de amasado, sin producir segregación cuando se utilizan como fluidificantes. *Disminuyen la cantidad de agua de amasado para una trabajabilidad dada, cuando se utilizan como reductores de agua. *Pueden crear a la vez ambos efectos. | *Aditivo que puede ir en sinergia con el aditivo principal “Superfluidificante”., nunca debe utilizarse individualmente. *Conviene conocer la naturaleza química de estos ya que pueden afectar notablemente el desarrollo de la velocidad de fraguado | ||||
Superfluidificantes/Reductores de agua de alta actividad | *Aumentan, de forma significativa la trabajabilidad para una relación (Agua/Cemento) dada (manteniendo constante la cantidad de agua) *Cuando se utilizan como superfluidificantes. producen una reducción considerable de la cantidad de agua de amasado, para una determinada trabajabilidad. *Cuando se emplean como reductores de alta actividad obtienen simultáneamente ambos efectos. | *Aditivo principal en el diseño de un hormigón para pavimentos. *Las características que aportan al hormigón no sólo deben estar relacionadas con la reología o la reducción de agua, sino que deben poseer la capacidad justa de aumentar la migración de finos a la superficie. *Por estas razones se debe recurrir a superfluidificantes diseñados específicamente para hormigones de pavimentos no los que se usan genéricamente. | ||||
Moduladores de la Viscosidad | *Disminuidores y mejoradores de la viscosidad alta en hormigones de altas prestaciones que permiten acercar los mismos a la reología objetiva. | *Solo son adecuados para hormigones con altas viscosidades y en los que no sea posible disminuir la misma por métodos simples. *Utilizarlos en la sinergía química puede resultar muy peligroso si no se conocen sus posibles efectos en la masa |
🡪Modificadores del tiempo de fraguado y/o endurecimiento | ||||
Tipo | Características | Idoneidad para uso en hormigones de pavimentos | ||
Aceleradores de fraguado | Reducen el tiempo de fraguado del cemento. | *Pueden utilizarse en ciertas ocasiones, temperaturas o entornos fríos o calientes que requieran modificar la velocidad de fraguado. *Algunos Superfluidificantes ya disponen de ciertas cantidades de estos compuestos con lo que no habrá que utilizarlos individualmente si es necesario y primordial saber cuales pueden ser sus efectos y causas | ||
Retardadores de fraguado | Retrasan o aumentan el tiempo de fraguado del cemento | |||
Aceleradores de endurecimiento | Aumentan o aceleran el desarrollo de las resistencias mecánicas iniciales |
2.CLASES DE ADITIVOS QUE NO DEBEN UTILIZARSE EN LA CONFECCIÓN DE HORMIGONES PARA PAVIMENTOS
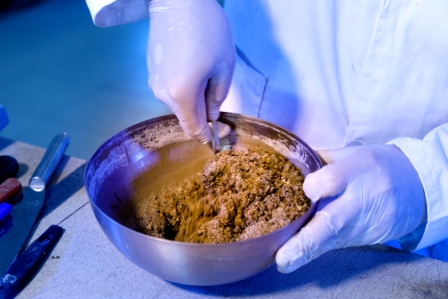
🡪Modificadores del contenido de aire o de otros gases | ||
Tipo | Características | Idoneidad para uso en hormigones de pavimentos |
Inclusores de aire | Incluyen en la masa un número elevado de microburbujas de aire, separadas y repartidas uniformemente, las cuales permanecen durante el endurecimiento del material. | Ninguno de estos aditivos debe utilizarse a no ser que las características de los materiales o la peculiaridad del vertido, bombeo o producción en obra lo requieran. |
Generadores de gas | Producen un gas (por ejemplo, hidrogeno, oxigeno, nitrógeno, etc.) que queda enmayor o menor parte incluido en la masa. | |
Generadores de espuma | Producen, por medios mecánicos, una espuma estable formada por burbujas de aire de tamaño variable, que se encuentran homogéneamente distribuidas dentro de la masa a la que confieren estructura alveolar. | |
Desaireante o antiespumantes | Eliminan el exceso de aire introducido en la masa mediante el empleo de ciertos áridos o aditivos utilizados para obtener otra función principal, distinta a la introducción de aire. |
3.CLASES DE ADITIVOS QUE PUEDEN UTILIZARSE CON ESTUDIO TÉCNICO PREVIO EN LA CONFECCIÓN DE HORMIGONES PARA PAVIMENTOS

🡪Aditivos que mejoran la resistencia a las acciones físicas | ||
Protectores contra las heladas | Suelen ser inclusores de aire, aceleradores de fraguado o de endurecimiento. | Solo deben utilizarse en casos de pavimentaciones exteriores con riesgos de heladas siempre estudiando la interacción que estos aditivos puedan realizar y que las condiciones lo exijan. |
Anticongelantes mejoran la resistencia a la congelación | Disminuyen el punto de congelación del agua de amasado, impidiendo, además la aparición de cristales de hielo en el hormigón, mortero o pasta enestado fresco | |
Reductores de penetración del agua. | Incrementan la resistencia al paso de agua bajo presión a través de las mezclas endurecidas. | No son aconsejables debido a la interacción superficial que generan con las capas de rodadura/dryshakes. |
Hidrófugos o repulsores de agua | Disminuyen la capacidad de absorción capilar o la cantidad de agua que pasa a través de una masa saturada y sometida a un gradiente hidráulico. | |
🡪Aditivos que mejoran la resistencia a las acciones físicoquímicas | ||
Incrementan la resistencia de los conglomerados, así como de las armaduras, a los ataques de naturaleza fisicoquímica internos o externos. | ||
Inhibidores de corrosión de armaduras | Reducen la posibilidad de corrosión de las armaduras embebidas en el hormigón o mortero. | Se pueden utilizar en casos de necesidad de proteger armaduras o inhibir la reacción álcali-áridos siempre y cuando no haya interacciones con la reología del hormigón y la puesta en obra. |
4.Requisitos exigibles a aditivos para hormigones-concretos de pavimentos de altas prestaciones y altas exigencias
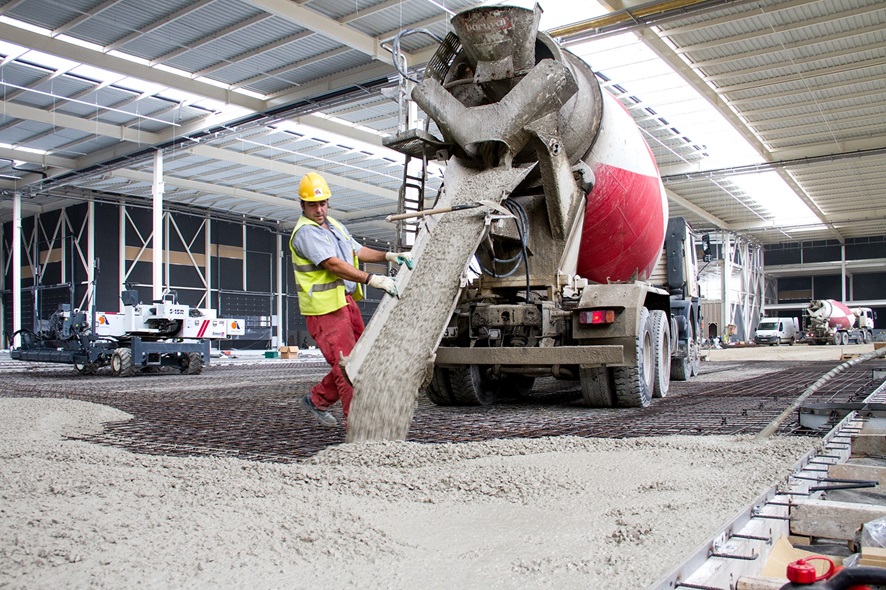
Antes de nada recordemos que existen «ocho elementos reológicos básicos» a tener en cuenta en la reología de una masa de hormigón-concreto, Para obtener una buena e incluso óptima masa de hormigón-concreto fresco que hacen, entre ellos, una relación única e indivisible, haciendo que esa masa fresca pase a ser, una vez endurecida, un conglomerado de “altas prestaciones y altas exigencias” como pavimento.

Estos «ocho elementos reológicos básicos» se describen en la siguiente tabla:
Elemento | Detalle |
Docilidad-Fluidez-Consistencia y su evolución | La docilidad del hormigón habrá de ser la necesaria para que, con los métodos previstos de puesta en obra y compactación, el hormigón rodee las armaduras con continuidad, con los recubrimientos exigibles, y rellene completamente los encofrados sin que se produzcan coqueras. En general, la docilidad del hormigón se valorará determinando su consistencia por medio del ensayo de asentamiento, según la norma UNE-EN 12350-2, excepto para los hormigones autocompactantes, según el artículo 33.5 Código Estructural CodE español. |
Viscosidad | Es la propiedad física que evalúa las colisiones de las partículas de la pasta de mortero cuando se mueven a diferentes velocidades provocando una resistencia a su movimiento. Se mide con un viscosímetro/reómetro en cPs o Pa . Esta característica se define en el Código Técnico Estructural CodE español para hormigones autocompactantes (Tabla 33.6.b Clases de viscosidad AC-V), pero para hormigones dedicados a pavimentos que requieren módulos de viscosidad medios o bajos no se contempla. |
Cohesividad | Es la capacidad de fuerza de atracción entre partículas de la pasta de mortero. La cohesión mantiene juntas a las partículas de esa suspensión. Se mide la determinación al esfuerzo con viscosímetro/reómetro en cPs o Pa y no viene especificada en el Código Estructural CodE español. |
Tensión superficial | Se define como la propiedad que tiene la masa gelificada para resistir la fuerza de la gravedad; y es clave para determinar la compatibilidad en la intersección de la capa de rodadura con el hormigón. Es consecuencia de las fuerzas cohesivas(cohesividad) entre las propias partículas de la suspensión de la pasta de mortero. Debido a la tensión superficial se forma una película de superficie, que hace más difícil incorporar un elemento externo ajeno, como es una capa de rodadura, o cualquier endurecedor para generar superficies monolíticas. |
Temperatura y su evolución | Medir la evolución de la temperatura interna y externa de la pasta de mortero durante el tiempo que sea necesario dará pistas de la cristalización interna y la madurez que se va formando, permitiendo además evaluar riesgos por altas o bajas temperaturas. |
Velocidad de fraguado | Evaluar la velocidad de fraguado permitirá conocer las ventanas de tiempo de las que se dispondrán en la producción en obra. Una vez conocidas y, si es posible, se adecuará el diseño del hormigón teniendo en cuenta las mismas. |
Cambio de volumen | Evaluar el cambio de volumen que pueda haber (expansión-retracción) permitirá diseñar hormigones más estables, con menor tensión, y compensar la misma con la química, así como realizar ajustes en el diseño o sistemas adecuados. |
Aire ocluido | Se denomina aire ocluido a las burbujas de aire microscópicas (generalmente esféricas de 0,1 a 1 mm de diámetro) que se introducen de forma intencionada en el mortero u hormigón durante la mezcla. En estado fresco, las burbujas de aire (<3-4% del total de la masa) actúan como lubricante y hacen la mezcla más manejable. Una vez endurecido el hormigón, las burbujas de aire permiten oscilaciones térmicas en el hormigón sin perjudicar su durabilidad; si se disponen en la masa de niveles >4% se corre el riesgo de tener acabados irregulares, llenos de coqueras, además de poder también perjudicar la resistencia final. |
Todos los aditivos que se utilicen en un hormigón-concreto de pavimentos deben cumplir los siguientes requisitos:
- Cumplir la UNE EN-934-2 y estar documentados con la clasificación oportuna, un certificado del fabricante que garantice que el producto satisface los requisitos prescritos en la citada norma, el intervalo de eficacia (proporción a emplear) y su función principal para el desempeño objetivo.
- Autorización por parte de la Dirección Facultativa, el Suministrador y el Contratista de Pavimentos.
- Deben ser líquidos y dosificados por instalaciones automáticas que aseguren dosificaciones precisas en cantidades y tiempos de entrada en los ciclos oportunos productivos.
- Deben estar almacenados en continentes que aseguren que no pueda haber contaminación con otras sustancias o deterioro por cambios de temperaturas, exposiciones a lluvias, sol o corrientes que puedan modificar las características de los aditivos.
- Deben ser, en la medida de lo posible, específicos para pavimentos de hormigón huyendo de aditivos genéricos con reologías no acordes a las necesidades de trabajabilidad y puesta en obra.
La industria química en sinergia con la industria química del cemento y del hormigón-concreto han realizado un magnífico trabajo de I+D+i con avances impensables a finales del Siglo XX para aportar tecnología puntera al mundo del hormigón preparado que durante décadas desarrollaron en el mundo del prefabricado del hormigón-concreto con metodologías más industrializadas, fáciles de parametrizar y observar su evolución.
Estos avances permitieron “altas prestaciones” en la fase fresca del hormigón-concreto y en la fase endurecida un sueño y anhelo que todo el profesional de hormigón pretende desde el inicio de su carrera, imitar a la naturaleza utilizando elementos naturales y toques de alquimia generando conglomerados análogos a características pétreas que se han ido creando durante miles de años en su ciclo litológico.
En un entorno tan controlado como es la industria del prefabricado de hormigón-concreto se puede lograr, pero en una industria tan sumamente dependiente de factores exógenos como es la industria del hormigón-concreto preparado, este es un reto altamente difícil de conseguir con una total efectividad y total homogeneidad en todo el suministro.
Tengamos en cuenta que el hormigón-concreto fabricado en central es un material heterógeneo a pesar de todos los medios productivos y técnicos que dispongamos tenemos que tener en cuenta que aminorar esa heterogeneidad es una cuestión que no todos los fabricantes están preparados para conseguir; unos debidos a su falta de recursos técnicos o humanos, otros por entorno, mercados y faltas de exigencias en su suministro, otros por otros motivos en los cuales no entraremos a detallar y que suponen un agravío al colectivo de fabricantes de hormigón-concreto representados en Anefhop y que si son ejemplo de buen hacer industrial.
5.Reología y la importancia de los aditivos en la masa de un hormigón-concreto para pavimentos

Si pretendemos entrar más a fondo en las necesidades que deben tener los aditivos principales de un hormigón-concreto debemos comprender antes entender lo que es la importancia de la temática de la reología en las pastas de cemento.

Teniendo en cuenta que la reología es uno de los puntos que consideramos fundamentales, para explicar de qué se trata resumiremos un estudio “Aportaciones al estudio reológico de pastas y morteros de cemento portland” Universidad Sevilla(J.MIRANDA, Dpto. de Ingeniería Química./V. FLORES-ALÉS, Dpto.de Construcciones Arquitectónicas/J. BARRIOS, Dpto. de Construcciones Arquitectónicas). Publicado en MATERIALES DE CONSTRUCCIÓN, Vol. 50, nº 257, enero/febrero/marzo2000. Consejo Superior de Investigaciones Científicas Licencia Creative Commons 3.0 España.
Este trabajo es sin duda una perfecta explicación de porqué la reología es un punto clave y porqué hemos de estudiarla previamente en la pasta de mortero antes de trasladarla al hormigón-concreto. No encontramos una explicación tan sencilla, clara y concisa de esta temática.
El hormigón-concreto se puede considerar como una suspensión de partículas sólidas gruesas en una suspensión de partículas finas. La reología de esta última influye sustancialmente sobre el comportamiento del hormigón-concreto, de ahí la importancia de realizar un estudio sobre la reología de pastas y morteros.
La reología de pastas y morteros de cemento ha sido objeto de múltiples estudios. Sin embargo, este comportamiento no ha sido todavía totalmente explicado. De hecho, los datos existentes de diferentes autores son a menudo inconsistentes y contradictorios. Esto es debido, probablemente, al complejo comportamiento reológico de estos materiales, por la gran cantidad de factores de los que depende, y al desarrollo con el tiempo de los procesos de hidratación de los componentes del cemento.
El comportamiento y propiedades finales de un hormigón-mortero dependen de numerosas variables como son:
- Calidad de cemento, arena, agua y aditivos usados (Calidad de la pasta de Mortero)
- Proporciones de la mezcla.
- Forma, duración y temperatura del amasado.
- Condiciones de humedad y temperatura de su conservación.
Los ensayos reológicos sobre morteros de cemento son difíciles de llevar a cabo debido al tamaño de los áridos, por lo que se han de comparar diferentes sistemas de medida para poder definir el verdadero comportamiento reológico de las muestras.
Desde Betonia aconsejamos hacerlo solo con la pasta de mortero que es la suma de las cantidades de cemento, arena/s, aditivos, agua/s que contenga o se aporten al material( humedades de los materiales y las diferentes aguas aportadas) y finalmente el aire ocluido que contenga esa masa.

La microestructura de la pasta de cemento en estado fresco se basa en las uniones que se crean entre partículas sólidas que en el momento del primer contacto agua-cemento se encontraban tocándose. Alrededor de las partículas se forma una capa de material hidratado que las mantiene unidas formando flóculos en forma de platos o de esferas.
El endurecimiento de la pasta de cemento Portland y su acción cementante es resultado esencialmente de la formación del gel de tobermorita, pues las pastas preparadas con los silicatos tricálcico y bicálcico fraguan y endurecen de igual forma que las preparadas con cemento Portland y las resistencias finales desarrolladas por ambas fases minerales son prácticamente iguales.
Asimismo, el proceso de hidratación o fraguado de los cementos da lugar a la formación de estructuras complejas, integradas también por diversas especies minerales hidratadas que conforman básicamente un gel formado por partículas microcristalinas de dimensiones coloidales que determinan, en gran parte, las propiedades de la roca de cemento endurecida.
El problema de la estructura de la pasta de cemento endurecida hace surgir cada vez el contraste entre la hipótesis de Le Chatelier, sobre la naturaleza cristalina de aquélla, y la de Michaelis, sobre el carácter de gel de la misma. Actualmente, se acepta una síntesis de ambas, al ser considerada la estructura como un gel formado de partículas microcristalinas de tobermorita, las cuales, en determinadas circunstancias, pueden aumentar su grado de cristalización.
La formación de la estructura del gel microcristalino define las resistencias mecánicas debidas al proceso de hidratación de los cementos en los morteros, estructura que comienza a formarse desde el inicio de la reacción, aunque la manifestación de la resistencia mecánica implica la presencia de un período de inducción, tomándose cada vez más densa y compacta.
En el caso de los morteros o pastas de mortero, la complejidad se acentúa grandemente, dado que el cemento se hidrata en presencia de otras sustancias minerales, tales como los áridos, que aportan sus propias características mineralógicas, granulométricas y morfológicas. Además, hay que considerar la adición de cantidades de agua variables, así como el procedimiento de preparación y ulterior curado del mortero.
El hidrogel ideal es así modificado por la introducción de una fase sólida heterogénea. Cuando el tamaño de partícula del sólido es superior al espacio máximo intercristalino en el gel, este último puede ser considerado como un medio de suspensión de los áridos.”
Si controlamos esta fase de hidrogel y su reología tendremos a buen seguro la reología objetiva del hormigón que nos hará controlar casi con absoluta seguridad lo que pasa en ese mundo de suspensión de partículas sólidas gruesas en una suspension de partículas finas.
Para controlar la reología disponemos principalmente de unas herramientas-soluciones tecnológicas que tenemos a nuestra disposición como son los aditivos químicos y más concretamente los que hemos definido.
Partamos de una base clara y concisa: los aditivos químicos que la industria química aportan para pavimentos de hormigón en la actualidad van encaminados básicamente a cuatro objetivos:

- Mejora ra/c, que debe ser un objetivo en cierta medida, pero no debe confundirnos ya que necesitamos cierta cantidad de agua libre para poder hidratar la capa de rodadura y pulir con tranquilidad durante el proceso de pulido. Bajas r/ac generan hormigones viscosos y de reología poco trabajable y esto dificulta el amasado e intersección efectiva.
- Mejora Costes, anhelo de todo fabricante de hormigón-concreto preparado y que confunde las necesidades finales. No se pueden, ni se deben ofrecer aditivos genéricos para realizar pavimentos de hormigón, estos generan hormigones fuera del rango y necesidad objetiva.
- Evitar retrasos de fraguado, muchos aplicadores cansados de altos retrasos de fraguado (motivados generalmente por aditivos plastificantes) solicitan al fabricante de hormigón que no utilice aditivos y esto perjudica notablemente la reología. En otros casos se utilizan aditivos que provocan excesos de ralentización de fraguados o falsos fraguados en zonas específicas acabando por generar pavimentos fallidos.
- Mejoradores de acabados, que contienen motivadores de migradores de finos a la superficie generando superficies densas que retienen altas dosis de agua lo que generan delaminaciones genéricas. Todos los aditivos que vayan a hormigones-concretos de pavimentos deberían disponer de esta característica, pero en una medida que nos ayude no perjudicando y confundiendo el objetivo final como una bondad final.
Los fabricantes de aditivos españoles cuentan con una asociación nacional ANFHA que divulga, asesora e informa de las técnicas y usos de los aditivos y que recomendamos solicitar consejo si se desea sinergias químicas específicas y contrastadas para el uso en pavimentos de hormigón-concreto.
La normativa que ampara la clasificación de los aditivos es la UNE-EN 934-2: y las categorías son las siguientes: Reductores de agua-Plastificantes/Reductores de agua de alta actividad/ Superplastificantes/ Aceleradores de fraguado /Aceleradores de endurecimiento/Retardadores de fraguado/Inclusores de aire/Retenedores de agua/Hidrófugos en masa/Reductores de agua de alta actividad-Superplastificantes-Retardadores de fraguado/Reductores de agua-Plastificantes- Aceleradores de fraguado/Multifuncionales/Retardadores de fraguado-plastificantes-reductores de agua.
Los mismos fabricantes de aditivos disponen de portafolios de modificadores de la reología amplios y que cubren casi todos los espectros de aplicación a excepción de los hormigones para pavimentos de las que no hay respuestas claras sino opciones laxas maquilladas de mejoradores de la tensión superficial. Estas marcas cuentan con aditivos superfluidificantes que van en la línea correcta, pero necesitan entrar en sinergias con plastificantes-fluidificantes que logren esas reologías objetivas y eviten altas viscosidades y cohesividades que perjudican notablemente la trabajabilidad, es decir: por sí solos, no solo no funcionan, sino que pueden hasta perjudicar el desempeño.
Si analizamos más a fondo porqué estos aditivos se quedan a medio camino, debemos tener en cuenta que desde un punto de vista teórico: la cantidad de agua a añadir para la obtención de un hormigón determinado (supuesto el estado saturado/superficie seca de los áridos) coincidirá con la estrictamente necesaria para hidratar las partículas de cemento portland. En el citado supuesto ideal, el agua de amasado reaccionaria con dichas partículas transformándose en un sólido de casi nula porosidad y, consecuentemente, de alta resistencia.
La situación real difiere sensiblemente del supuesto anterior y para entender mejor el funcionamiento de estos aditivos se hace preciso recordar el comportamiento agua-cemento en el proceso de mezclado y fraguado del hormigón-concreto. Primero se forma la pasta aglutinante producto de la lubricación de las partículas de cemento y de árido tras la absorción del agua, y luego esta pasta se vuelve cementante producto de la reacción química que se lleva a cabo entre ambas al iniciarse el fraguado.
En la primera de estas etapas es cuando se produce la mezcla de los componentes y las primeras reacciones electroquímicas entre el agua y el cemento, apareciendo las características del hormigón fresco como trabajabilidad, docilidad, consistencia, etc.
Estas características están gobernadas principalmente por las reacciones electroquímicas producidas entre las moléculas de agua y los granos de cemento, los cuales poseen un gran número de iones en disolución en su superficie. Estos iones tienden a formar, debido a una afinidad electroestática, flóculos o capas de solvatación al entrar en contacto con el agua durante la operación de amasado.
Dichos flóculos ejercen dos efectos nocivos en la masa de hormigón:

Floculación de los granos de cemento en presencia de agua
1.- Impiden la dispersión uniforme de las partículas de cemento en la masa de hormigón.
2.- Retienen una determinada cantidad de agua en el interior de su masa que incidirá negativamente en la porosidad final del material.
El agua retenida no es utilizable para lubricar la masa de hormigón ni para contribuir a la hidratación de los granos de cemento, lo que implica la necesidad de incorporar una cantidad adicional sustitutoria. Esta agua adicionada, al no poder reaccionar con los granos de cemento anhidro, origina al evaporarse un incremento de la porosidad de la pasta de cemento que implica una cierta perdida de resistencia del hormigón endurecido y un aumento de su permeabilidad.
Dado que la relación (Agua/Cemento) «r a/c- w/c» de un hormigón-concreto tiene una importancia trascendental en las características de este, especialmente en sus resistencias mecánicas, interesa que en los hormigones-concretos esta relación sea lo más baja posible, pero esto conlleva ciertas dificultades como son un sistema de mezclado muy eficaz para conseguir una mezcla homogénea y el disponer de medios de compactación muy enérgicos.
Con el empleo de aditivos mejoradores de la reología pueden eliminarse estos inconvenientes sin necesidad de aumentar la cantidad de agua de amasado.
🡪Fluidificantes/plastificantes
Los efectos nocivos de la floculación de las partículas de cemento ya se venían contrarrestando, al menos parcialmente, mediante la incorporación a la masa de hormigón de aditivos reductores de agua o fluidificantes que son productos químicos de naturaleza orgánica(generalmente lignosulfonatos, ácidos hidroxicarboxílicos y sales e Hidratos de carbono) formados por macromoléculas tensoactivas capaces de neutralizar las cargas eléctricas de los granos de cemento y, por consiguiente, su capacidad de floculación.
Dichas macromoléculas tensoactivas tienen un extremo de su cadena hidrófilo con afinidad por el agua y otro hidrófobo repulsor del agua (Grupos polares aniónicos), con lo cual quedan adsorbidas y orientadas en la superficie de los granos del cemento. Como resultado de la capa de dipolos de agua fijada se impide la reunión o coalescencia de los granos del cemento actuando como un lubricante y obteniéndose un sistema bien dispersado. Así mismo, liberan el agua atrapada entre los flóculos del cemento que queda disponible para aumentar la fluidez del hormigón.

Esquema de actuación de los fluidificantes
Utilización de fluidificantes/plastificantes polifuncionales en hormigones para pavimentos | |
Ventajas | Inconvenientes |
-Aumentar la docilidad sin incrementar la cantidad de agua de amasado. -Reducir la relación en torno a un 10-15% (Agua/Cemento) a igualdad de docilidad. -Reducir la tendencia a la segregación del hormigón durante el transporte y disminuir la exudación. -Mejorar la adherencia del hormigón a las armaduras. -Incrementar la resistencia a compresión (10-20 % a los 28 días), al permitir reducir el agua de amasado. -Aumentar la durabilidad y resistencia a la abrasión final. -Retardar ligeramente el fraguado. -Ayuda al transporte por bombeo | -Posible aumento de la retracción. -Inclusión de aire, sobre todo por los tipos lignosulfonatos -Retardos muy importantes en el fraguado y disminuciones de las resistencias iniciales, agravándose en temperaturas bajas dan lugar a una especie de «falso fraguado» especialmente cuando se emplean dosis altas de los mismos o cuando el cemento contiene poco yeso. -Alta inclusión de aire. -Eficacia baja o nula en hormigones con bajas relaciones de (Agua/Cemento). -Con determinados cementos genera delaminaciones en los endurecedores denominados capas de rodadura. |
🡪Superfluidificantes
Los superfluidificantes modifican la reología de los hormigones y van más allá que los fluidificantes-plastificantes permitiendo conseguir mezclas muy dóciles y fáciles de poner en obra, sin reducir, sus resistencias, hormigones de docilidad normal, pero con muy bajo contenido de agua, hormigones en los que se conjuguen las dos características anteriores, es decir, buena docilidad y menor cantidad de agua de la normal, hormigones con reducida dosificación de cementos pero que poseen resistencias y docilidad normales.
Los superfluidificantes son productos que se han desarrollado hace décadas (comenzando por los policondensados de formaldehido y melamina sulfonada SMF o de formaldehido y naftaleno sulfonado SNF y lignosulfonatos modificados MSL) que permiten conseguir reducciones de agua de amasado de hasta el 25% (2,5 veces más que los fluidificantes), sin tener los inconvenientes reseñados. Este tipo de aditivos también se conocen con los nombres de «superplastificantes» y «reductores de agua de alta actividad”.
En la actualidad existen diferentes tecnologías que han sustituido a las anteriormente descritas:
- Polímeros de policarboxilato (PCE) de cadena principal corta con alta densidad de largas cadenas laterales para obtener aditivos con alta capacidad de reducción de agua y rápido desarrollo de resistencias iniciales más encaminados a la industria del prefabricado y hormigones de obras grandes civiles que requieran altos desempeños con resultados casi inmediatos. Estos aditivos no deben considerarse para hormigones de pavimentos principalmente por que su principal característica es conseguir altas capacidades de reducción de agua y rápido desarrollo de resistencias iniciales, generando altas viscosidades plásticas y escasa trabajabilidad tras su fabricación.
- Polímeros de policarboxilato (PCE) con cadenas principales de alto peso molecular, con menor densidad de cadenas laterales y de menor longitud, e incluso introduciendo grupos funcionales para el control de la velocidad de absorción sobre el cemento que permiten mejores consistencias y mantenimientos de las mismas, avanzando también en la bajada inmediata viscosidad plástica alta.
- Polímeros de naturalezas varias con diferencias importantes en la composición de la cadena principal y especialmente en los grupos funcionales de anclaje en los cuales su mecanismo de absorción está dirigido por interacciones de menor rigidez. Cuentan con activadores mejoradores de acabado que permiten una menor tensión superficial, un mayor mantenimiento de la consistencia y una bajada de esa inmediata viscosidad plástica alta, que aunque parezca suficiente aún requiere de un camino arduo para conseguir controlar ese mantenimiento y poder rebajar esa viscosidad.
Cuando estos superfluidificantes se integran en la masa se absorben sobre las partículas de cemento y les imparten una carga negativa, que disminuye de forma considerable la tensión superficial del agua que las rodea, además de producir una repulsión entre ellas evitando su floculación, con lo que se mejora la fluidez del sistema permitiendo el recubrimiento total de las partículas de cemento incorporándolas cargas de signo negativo que, neutralizando las fuerzas de atracción electrostáticas existentes entre dichas partículas, facilitando extraordinariamente el fenómeno de floculación.
Su efecto multiplica el efecto de los tradicionales fluidificantes-plastificantes, por ello, el empleo de un aditivo súper plastificante, de elevada calidad, será más capaz de dispersar los gránulos del cemento con componentes secundarios, mejorando la cohesión y la facilidad de bombeo del hormigón, sin causar los típicos problemas de efecto colchón, así como el fenómeno de delaminación por la falta de adherencia de la capa de rodadura a dicho hormigón.
Utilización de superplastificantes en hormigones para pavimentos | |
Ventajas | Inconvenientes |
-Mejora plausible del comportamiento reológico de los hormigones gracias a la reducción de la viscosidad plástica de aportan. -Aumentar la docilidad sin incrementar la cantidad de agua de amasado en un 30%-40% respecto a los plastificantes-fluidificantes. -Permiten, en ocasiones, la producción de hormigones de baja viscosidad y excelente trabajabilidad, incluso con bajos contenidos de cemento, finos y agua. -Mejora el paso por bomba, bajando la presión <100 Bares, aumentando la productividad. -Permiten fabricar hormigones con óptimas resistencias mecánicas y durabilidad con reducido contenido de cemento y agua. -Extendidos más fáciles y rápidos, con tiempos de vibrado del hormigón es menor. -Mejorar la adherencia a las armadurasIncrementar la resistencia a compresión (10-20 % a los 28 días), al permitir reducir el agua de amasado. -Aumentar la durabilidad y resistencia a la abrasión -Ayuda al transporte por bombeo -Reducción de su huella de CO2 | -Posible aumento de la retracción de manera inmediata. -Aceleramientos súbitos muy importantes en el fraguado y aumentos de las resistencias iniciales, agravándose en temperaturas altas dando lugar a una especie de «final del inicio de fraguado (F.F.)» especialmente cuando se emplean dosis altas de los mismos o cuando el cemento contiene alto porcentaje de Clinker. -Riesgos de sobredosificación con mínimos porcentajes al tener tanta eficacia que generan segregaciones, sedimentaciones, etc. -Altas cohesividades al igual que altas viscosidades dinámicas y cinéticas. |
Esta es la teoría, pero en la realidad estos productos además de aportar todas las ventajas comentadas también por el contrario pueden llegar a perjudicar notablemente la reología de los hormigones volviéndolos altamente cohesivos con lo que la trabajabilidad en obra en el momento del proceso de pulido genera altas tensiones superficiales que hace que el cristal en la intersección entre la capa de rodadura y el hormigón se vea comprometida formando microfisuras, delaminaciones y demás patologías dañinas.
En la gran mayoría de los casos la reología ya está fuera de uso recomendado en el momento de su llegada a obra antes del vertido con lo que obligamos al hormigón a magreos continuos en una fase ya avanzada del inicio del fraguado que hace que el hormigón en esta fase nuclear inicial se vea atosigado con tensiones continuas que afectarán a buen seguro a su desempeño.
Analizando los desempeños en los cuales se mueven los diferentes aditivos podemos obtener un espectro completo del diseño por el cual los fabricantes se guían para proponer aditivos para el hormigón y sus diferentes aplicaciones.

En estos gráficos podemos comprobar una paradoja que muy pocos profesionales han reflexionado: Un superfluidificante nos ayuda sin duda a mejorarar muchas características en el hormigón, pero perjudica notablemente la reología, por el contrario, una plastificante mejora la reología, pero no tiene suficiente potencia para desarrollar los desempeños marcados.
Un Hormigón para pavimentos necesita trabajabilidad, soltura, mantenimiento de la consistencia durante el proceso de pulido y una vez avanzado el mismo una velocidad de fraguado constante y homogéneo que permita acabar el pulido sin retrasos, “islas de fraguado” o efectos colchón.
Nosotros desde hace años mantenemos que podemos realizar una sinergia entre ambos tipos de aditivos siempre y cuando cada uno sea compatible con el otro, no afecten a otros que participen en el cometido, cumplan unas características específicas y no afecten al diseño final.
Durante años en Betonia hemos realizado multitud de ensayos con diferentes materiales comparando la diferente reología y la evolución de esta según utilicemos unos aditivos u otros. Para ello hemos aprovechado durante todas esas pruebas de pasta de mortero a medir el esfuerzo de que dicha pasta de mortero muestra a su destrucción estructural en un viscosímetro/reómetro, con efecto cizalla y midiendo su curva de flujo resultante a un comportamiento plástico que podamos ponderar y evaluar, de esta forma existe una relación lineal entre el par de torsión que es proporcional a la resistencia viscosa sobre el eje sumergido, y, en consecuencia, a la viscosidad del fluido.

Se mide la viscosidad captando el par de torsión necesario para hacer girar a velocidad constante un husillo inmerso en la muestra de fluido a estudiar.
V=K x L
Siendo K un coeficiente que depende de la relación velocidad / vástago-husillo utilizado y L el valor medio de las lecturas dadas como válidas. También vale tomar la lectura media como válida ya que a nuestro parecer es una lectura correcta
Para ello hemos comprobado que el vástago/husillo adecuado para medir pastas de mortero es el R5(diámetro 21,34 mm de grosor y 134,29 mm de altura), un Eje 4 y a una velocidad de 100 rpm.
Todo queda registrado en nuestra Instrucción interna ITG-07.04/067 disponible que asegura tras comprobar la metodología, ratificar una buena repetibilidad; y utilizar un procedimiento adecuado para que no se den fenómenos de deslizamiento en las paredes de éste obtengamos lecturas que pueda interpretarse y nos sirvan para determinar con seguridad la reología de estas pastas de mortero.
6.Condiciones exógenas y del entorno para la elección de cada tipo de aditivo

Unido al hándicap de no tener respuestas claras de aditivación química para este tipo de hormigones-concretos, podemos sumar un factor clave y determinante como son las condiciones exógenas y de los entornos en los cuales se desarrolle la obra y vaya a descansar el futuro hormigón, elevando aún más la dificultad del diseño y ajuste previo.
El hormigón-concreto es un elemento que no es estanco, ni nada lo estanca y que depende de los factores ambientales. Se comporta diferentemente en ambientes invernales a bajas temperaturas, que en ambientes calurosos de verano con hormigones que pasen de los 30ºC o en ambientes húmedos con alto punto de rocío que generen microlluvias continuas, etc.
También podemos tener en cuenta que ese entorno puede ser cambiante, bien por condiciones climatológicas o bien porqué la obra se encuentre en un ambiente protegido como son las naves industriales actuales. Éstas, están hechas con cerramientos de panel de hormigón prefabricado y cubierta, que aíslan el entorno de la temperatura exterior: en verano, nos encontraremos con una temperatura interior más baja que en el exterior y en invierno al contrario será más alta, contando siempre con mayor humedad que la que pudiera haber en el exterior ya que dicho continente genera un efecto nevera guardando toda la humedad que procede de la evaporación del hormigón, de la preparación del terreno, etc. y generando como hemos mencionado antes corrientes invisibles de microlluvia continuas.
Este fenómeno nos obliga a estudiar no solo la temperatura del entorno en la que vaya a fabricarse y transportarse el hormigón, qué sin duda le afectará, sino que además debemos tener en cuenta la temperatura y humedad ambiente que habrá en la obra que será la que sin duda gobierne el desempeño del hormigón, siempre y cuando se cumplan tres máximas:
- Busquemos, en la medida de lo posible, la mayor homogeneidad de la dispersión de la masa mediante «controles de ajuste y/o lavado en vía seca» y «en vía húmeda controles de amperímetro o watímetro rigurosos en cada ciclo» en cualquiera de los dos sistemas siempre debe haber una supervisión de la idoneidad del suministro en la salida de planta. Recuerde: un buen hormigón-concreto en la salida de planta será un buen hormigón-concreto en la llegada (salvo que haya un accidente, un aporte de agua, una demora, etc) y sin duda un mal hormigón-concreto en la salida lo será en la llegada y si se arregla será a base de aditivación o aporte de agua extra en estado de reamasado y fase avanzada de fraguado. Seleccione aquellas sinergías químicas que le procuren esa dispersión de la masa objetiva fehacientemente.
- El tiempo de transporte tras fabricar el hormigón-concreto no debe superar los 30 minutos y debemos evitar carencias continuas de suministro, demoras ó paradas entre el mismo que generen juntas frías o empalmes de masas en diferentes estados de gelificación. De nada nos vale disponer de una gran calidad cualitativa de hormigón-concreto si la calidad cuantitiva es fallida ya que generaremos esas problemáticas típicas descritas con resultados desastres diversos en la losa de continuidad, planimetría, acabados, etc. Si por el contrario la planta está muy cerca de la obra, debemos procurar un excelente amasado en planta bien con amasados más efectivos en vía húmeda, bien con batidos más enérgicos en planta durante un tiempo mínimo de 5-10 minutos que aseguren la mayor homogenedidad y dispersión de la masa posible. En cualquiera de los dos casos haga una planificación de la ruta de transporte previamente al inicio de la obra y evalúe el tiempo de duración de entrega de los camiones, los pasos de tráficos complejos, las entradas y pérdidas de tiempo en obra, las zonas de lavado de los camiones en el retorno, etc. Toda pérdida de tiempo en la rueda de transporte puede afectar a la homogenidad del suministo, sobre todo en gradientes calurosos. Seleccione aquellas sinergías químicas que le procuren esa trayecto logístico con total seguridad de entrega objetiva.
- Dotemos al hormigón-concreto de la característica de mantenimiento de la consistencia objetiva al menos en la suma del tiempo de transporte y el tiempo de vertido garantizando que durante ese periodo de tiempo apenas pierda las características del diseño objetivo o perdiendo menos del 20% para evitar falta de homogeneidad y problemáticas diversas. Seleccione aquellas sinergías químicas que le procuren ese mantenimiento de la consistencia objetiva fehacientemente.
Estos condicionantes además nos hacen tener en cuenta que no existen soluciones “ad hoc”, sino que tengamos que innovar y buscar soluciones que palien en parte los inconvenientes de las diferentes temperaturas y entornos combinando varias técnicas de aditivos y métodos técnicos que actúen también sobre el mantenimiento de la consistencia, la velocidad de fraguado, la reología, etc. no olvidando que cada caso requiere recursos específicos y que dependerán en gran medida del conocimiento de los actores, de una disposición cooperativa, de una disciplina férrea, de una motivación y actitud conjunta de querer y creer que ese hormigón-concreto tenga los mayores cuidados en un entorno favorable facilitando en la medida de lo posible.
Antes de plantear soluciones debemos entender los dos tipos extremos de temperaturas-gradientes que pueden afectar al hormigón y las consecuencias que puedan durante y una vez acabada la obra.
Según el Artículo 71.5.3.1 de la Instrucción de Hormigón Estructural, la temperatura de la masa de hormigón, en el momento de verterla en el molde o encofrado, no será inferior a 5 °C y se prohíbe verter el hormigón sobre elementos (armaduras, moldes, etc.)
Temperaturas Calientes | Temperaturas Frías | |
Definición | Cualquier combinación de alta temperatura ambiente, baja humedad relativa, velocidad del viento y radiación solar, que afecte la calidad de la mezcla fresca o de la masa cementicia endurecido. En algunos documentos se complementa la definición anterior citando la temperatura mínima que debe exhibir la mezcla para que se dé la condición de concreto en clima cálido, el valor es 29ºC. Sin embargo, , un viento fuerte y rasante sobre una losa de hormigón puede provocar una desecación mayor que la radiación solar directa, de ahí lo conveniente de sopesar la suma de fenómenos expuestos en la definición. | Período en el que, por más de tres días consecutivos, se presentan las siguientes condiciones: -El promedio de temperatura diaria del aire es menor a 5ºC -Durante más de la mitad del día ó de un período de control de 24 horas la temperatura del aire no supera los 10ºC. |
Efectos directos en el hormigón | En estado plástico | |
*Demanda creciente de agua. *Velocidad creciente de pérdida de asentamiento con la correspondiente tendencia a agregar agua en obra. *Disminución del tiempo de fraguado, resultante en una mayor dificultad en la manipulación, terminado y curado, y aumentando la posibilidad de las uniones defectuosas entre una superficie y otra (juntas frías). *Tendencia creciente al agrietamiento en estado plástico. *Dificultad en el control del contenido de aire incorporado. | *El congelamiento del agua presente en los poros sufre un aumento de volumen del 9%, lo que sumado a otros mecanismos (difusión y presión osmótica), genera presiones internas de tracción. *Durante las primeras horas de vida del hormigón, el grado de saturación es inevitablemente elevado (se ha hidratado poco cemento). *El aumento de volumen producido por la congelación del agua destruye la estructura interna del material con pérdidas irreparables en la resistencia a larga edad (de hasta el 50%). | |
En estado endurecido | ||
*Disminución de resistencia debido a la mayor demanda de agua. *Tendencia creciente a la contracción por secado y agrietamiento térmico diferencial. *Disminución de la durabilidad. *Uniformidad decreciente de la apariencia superficial. | *Bajas resistencias finales -Baja dureza superficial -Partes de la masa sin finalizar etapa de fraguado con corrección *Agregados no envueltos y no adheridos a la matriz cementicia | |
Causas | *Empleo de cementos finamente molidos con mayor velocidad de hidratación que el cemento Portland Normal. *Empleo de hormigones-concretos con alta resistencia a la compresión, que requieren contenidos de cemento mayores. *Diseño de secciones esbeltas de hormigón con mayores cantidades de acero. *Aumento de capacidad de las cubas de hormigón. *Necesidad de mover grandes volúmenes de hormigón de bajo asentamiento sobre distancias verticales y horizontales mayores. *Mayor exigencia y consecuente desgaste del equipo de bombeo de hormigón. *Necesidad productiva y económica de realizar un trabajo continuado dentro de los horarios de mayor temperatura. | *Empleo de cementos lentos y no adecuados para estas temperaturas. *Materiales muy fríos que generan masas parcialmente congeladas. *Zonas de obra con exposición a corrientes o ambientes exteriores. +Subbases encharcadas de agua que está a temperatura fría y que genera altos retrasos de fraguado. |
En este gráfico definimos cuatro posibles casos de una obra protegida de plena exposición solar y corriente que pueda afectar a la desecación súbita de la superficie.
🡪Aditivos inhibidores de la velocidad de fraguado
Para este tipo de situaciones debemos contemplar estrategias diferentes con técnicas, herramientas y consejos siguientes para actuar sobre las matrices cementicias.
Una de las herramientas que nos aporta la tecnología es la de contar con aditivos acelerantes o retardantes para mitigar en cierta medida los efectos de esas temperaturas en las masas de hormigón-concretos.
La industria química ha dispuesto de soluciones individuales o conjuntas en un solo aditivo, que permiten contar con los beneficios de los mejoradores de la reología y además disponer de características modificadores de la velocidad del inicio de fraguado.
Son simples ayudas que sumadas a los diferentes ajustes del diseño nos pueden paliar, en cierta medida, los inconvenientes de un hormigón-concreto frío o caliente. Sin un correcto diseño su efectividad será efímera, insignificante y desde luego una temeridad que dispone todo el resultado a la suerte.
🡪Aditivos modificadores del fraguado y endurecimiento
Son aditivos que, dosificados a las pastas, morteros u hormigones-concretos en el momento del amasado, impiden, retardan o aceleran el fraguado de estos o actúan sobre su endurecimiento; a estos aditivos se les denomina inhibidores de fraguado, retardadores y acelerantes, respectivamente.
Los motivos por los cuales podemos necesitar acelerar o retrasar el hormigón son los siguientes.
Acción | Aditivo | Transporte | Producción | Características finales |
Retardo | Retardante | *Gran distancia o alto tráfico *Altas temperaturas con fraguados súbitos | Puesta en obra y ejecución con altas temperaturas | Control del proceso de fraguado paulatino, endurecimiento y posterior curado |
Aceleramiento | Acelerante | *Bajas temperaturas que afecten a fraguados muy lentos | Puesta en obra y ejecución con bajas temperaturas | Necesidad de altas resistencias, endurecimientos y madureces iniciales que permitan producciones sin retrasos importantes. |
🡪Aditivos Retardantes
Son sustancias que retardan la disolución de los constituyentes anhidros del cemento o su difusión.
La acción principal de los retardadores es aumentar el tiempo durante el cual el hormigón-concreto es trabajable permitiendo: el transporte de este sin que se produzca un endurecimiento prematuro o la segregación, lo cual es importante en el transporte a largas distancias, en hormigones bombeados, etc.; controlando el principio de fraguado de una masa para conseguir que el vertido de un área de hormigonado en varias fases fragüe al mismo tiempo sin dar lugar a discontinuidades o juntas; hormigonar en tiempo caluroso al hacer al cemento menos activo en su hidratación con lo cual desprenderá menos calor durante la misma.
Los retardadores pueden actuar de dos formas distintas según su naturaleza; una es favoreciendo la solubilidad del sulfato cálcico, que de por si es retardador de fraguado y, la otra, formando sales cálcicas que son adsorbidas por las partículas de cemento, retrasando de esta forma su hidratación.
Pueden estar presentes como aditivos individuales o formar parte de uno de los aditivos protagonistas de la sinergia en forma binaria o ternaria debido a su alta interacción a altas dosis y a su falta de interacción a bajas dosis. Se aconseja que actúen dentro de la sinergia participando en la reología y dotando a la misma de cierta dosis de retardo y control de la velocidad de fraguado inicial.
Se ha comprobado que los retardadores de fraguado influyen en el tamaño de los cristales formados de portlandita, ettringita,etc.
Los retardadores de fraguado aumentan la retracción de los hormigones, siendo el aumento dependiente de la dosificación del hormigón, y de las condiciones de curado de este.
Podemos dividir los retardantes fundamentalmente, incluyendo las sales en cinco grupos:
Grupo | Sustancias retardantes | Notas |
Grupo I | CaSO4.2H2O, Ca(ClO3)2, CaI2 | Solubilidad de la alúmina baja |
Grupo II | CaCl2, CaBr2, CaSO4.(1/2)H2O | incluye el cloruro de calcio y compuestos de similar naturaleza. Su comportamiento es similar a los del grupo III. Con este tipo de retardadores, la alúmina tiene una baja solubilidad a bajas concentraciones de retardador y la sal actúa como tal, pero a altas concentraciones, la solubilidad de la alúmina aumenta en la solución de cemento y no hay acción retardadora. |
Grupo III | Na2CO3, K2CO3, NaSiO3 | Compuestos carbonato de sodio y el silicato de sodio. Ambos reaccionan con el hidróxido de calcio para formar álcalis, y son responsables del pequeño efecto que producen, a la precipitación de hidróxido de aluminio, el cual puede ser disuelto a altas concentraciones. |
Grupo IV | -Surfactantes con grupos polares en la cadena hidrocarbonada, como por ejemplo gluconatos, lignosulfonatos y azucares. –Sales de sodio de los ácidos fosfórico, bórico y oxálico Na3PO4, Na2B4O7, Ca(CH3OOO), Sales de cinc o de plomo, como los óxidos | Son retardadores efectivos cuando son usados en pequeñas cantidades; ya que altas dosis prolongan excesivamente el periodo de fraguado, entrando una vez acabado en el periodo de endurecimiento de manera súbita. Su escasa dosificación puede inhibir parcialmente el proceso de fraguado de manera heterogénea por una falta de dispersión con falsos fraguados en partes de la masa. |
Grupo V | Sales del ácido fórmico y trietanolamina |
En nuestra opinión «solo si fuera estrictamente necesario retardar la velocidad de fraguado por altos gradientes en masa +35ºC, se podrán utilizar teniendo en cuenta que la dispersión de la masa debe ser altamente efectiva y probada, así como que además la dispersión del retardante también debe ser alta ya que si no lo fuera generaría islas y falsos fraguados.
🡪Aditivos Acelerantes
Son sustancias que, al contrario de los retardadores, favorecen la disolución de los constituyentes anhidros del cemento, su disolución o su velocidad de hidratación; su acción no está muy bien definida, aunque parece ser que provocan una cristalización rápida de silicatos y aluminatos cálcicos en la pasta del cemento hidratada. En una gran parte de ellos se encuentra el cloruro cálcico que es el acelerante por excelencia; sin embargo, también actúan como aceleradores o acelerantes el nitrato de calcio, el cloruro sódico, amónico, y férrico, las bases alcalinas, hidróxidos sódico, potásico y amónico, los carbonatos, silicatos y filosilicatos, aluminatos, boratos de sodio o potasio, el ácido oxálico, la alunita, la dietanolamina, trietanolamina etc.
En pavimentos de hormigón por el alto contenido de armaduras metálicas se descarta los acelerantes en base cloruros por su efecto corrosión y su disminución final en las resistencias finales. Debemos optar por aquellos que los que el contenido de ion cloro no es superior a 1 g/l y para ello la opción más recomendable es el Nitrato de Calcio Ca(NO3)2 que incrementa la velocidad de hidratación dando lugar a resistencias iniciales altas y a una gran liberación de calor en sus primeras horas, al actuar como catalizador en las reacciones de hidratación del aluminato del cemento, formando la sal de Friedel y acelerando la reacción entre el yeso y el C3A (Celita) y el C4AF (Felita).
Originalmente, el nitrato de calcio se utilizó como acelerador del fraguado exento de cloruros. Poco después se estableció como aditivo de hormigón («anti freeze») en ambientes fríos. Asimismo, su efecto acelerador se utilizó para compensar el retardo condicionado por los reductores de agua (fluidificantes). Además, a lo largo del tiempo se observó que el empleo de nitrato de calcio origina, en prácticamente todos los casos, una mejora moderada de la resistencia a largo plazo. Y finalmente también se constató un efecto de protección contra la corrosión para el acero de la armadura contra la corrosión inducida por los cloruros.

Pueden estar presentes en la masa como aditivos individuales o formar parte de uno de los aditivos protagonistas de la sinergia en forma binaria o ternaria debido a su alta interacción a altas dosis y a su falta de interacción a bajas dosis. Si forman parte de la formulación del aditivo protagonista (mezcla de polímero superfluidificante+nitrato de calcio) debemos tener en cuenta que la alta densidad 1,40-1,55 g/cm3 hace que sea aconsejable vigilar la suspensión de los sólidos ya que tenderán a decantar y generarán problemas dosificación en la producción de aditivos ya que al dosificar una suspensión con alta decantación estará dosificando solo la parte del polímero y del agua dejando el nitrato de calcio en el fondo haciendo que el aditivo dosificado no sea acelerante y dejando esa acción fuera de las características a aportar. Se recomienda instalaciones que aseguren una homogeneización constante con bombas o sistemas de recirculación o agitación en los acopios que eviten decantaciones.
Otro acelerante empleado frecuentemente es el carbonato sódico Na₂CO₃ también con una alta densidad 2,54 g/cm3; su dosificación debe ser estrictamente controlada debido a que en pequeñas dosis puede actuar como retardador. En cualquier caso, produce un aumento considerable de la retracción y más en hormigones con Cementos Tipo I y con agentes promotores de la expansión controlada por lo que desaconsejamos su uso.
El empleo de sosa NaOH o de potasa KOH es peligroso y no es aconsejable debido a que disminuye las resistencias mecánicas y aumenta la retracción.
Actualmente se están utilizando mucho los acelerantes a base de aluminato sódico NaAlO₂, de densidad más baja que los anteriores 1,5 g/cm3, por su gran eficacia y carencia de efectos secundarios; sin embargo, cuando el hormigón vaya a estar en contacto con terrenos ricos en sulfatos hay que tener en cuenta que la cantidad de aluminato será, en este caso, la suma de la del cemento y la del aditivo, pudiendo darse el caso de que el hormigón sea sensible al ataque, aunque se haya empleado un cemento SR.
🡪Consejos para temperaturas o entornos desfavorables
Consideramos que hay que estudiar todo el entorno siguiendo un método estricto de control ambiental para evaluar todos los posibles puntos que puedan ayudar o perjudicar al desempeño en la tabla siguiente reflejamos 8 puntos genéricos para cada tipo de temperatura, no obstante, recomendamos repasar a fondo todas las variables y optimizar los medios al máximo posible.
Uno de los puntos claves es conocer previamente el calor específico de cada material para poder realizar una previsión calorimétrica de cada receta (CalºC/g)), evaluando su proyección y establecer previamente medidas de corrección de la temperatura en cada proyecto de manera específica que nos permitirá conocer el aporte de agua caliente o agua fría que habría que hacer para calentar o enfriar la masa,
Cada material según su naturaleza, acopio o tratamiento tendrá una temperatura en cada momento, no obstante, nuestra experiencia de numerosas mediciones en diferentes ambientes y temperaturas arrojan estos promedios.

Es necesario no solo conocer el calor específico de cada material de manera individual sino también la cuantía final de la suma de todos que reflejará el calor de hidratación global y con ello preveer las acciones que sean necesarias para establecer el calor de hidratación a las necesidades productivas del pavimento.

También es necesario tener en cuenta que los niveles de absorción de los materiales y la velocidad con la que lo hacen en diferentes escenarios variando los mismos sin duda si están expuestos en los acopios expuestos a diferentes condiciones climatológicas.
La magnitud de la absorción es mayor para las arenas más finas debido a su mayor superficie específica, ahora, se observa también que a mayor temperatura los coeficientes de absorción son mayores. La diferencia en absorción entre 30 minutos y 24 horas se reduce al aumentar la temperatura; estas diferencias son casi nulas a las temperaturas más altas. Estas observaciones tienen consecuencias muy significativas para la trabajabilidad del hormigón en verano, ya que los agregados absorberán más agua en menos tiempo, ocasionando pérdidas de trabajabilidad y menores tiempos de fraguado.

Gráfico Velocidad de absorción de las arenas a diferentes tiempos
En este gráfico recogemos mediciones de absorción medias realizadas a diferentes arenas (naturaleza, morfología, tamaño y estado en acopio(secas-húmedas/frías-calientes) que reflejan la notable y decisiva influencia que ofrecen el aumento de temperaturas al aumento de absorción en las arenas que nos influirá directamente en el nivel de agua a aportar a la receta modificando la r a/c y la reología final.
Si observamos el gráfico tenemos un escenario más frío con 5ºC de temperatura en los materiales y parten con su nivel de absorción más común y según van aumentando en escalas de 5ºC el nivel de absorción aumenta un 5% hasta un total de+23% pasando de un nivel inicial de 2% a 2,45%. Esto nos hace reparar en la importancia de proteger en la medida de lo posible los acopios de los sofocos de las exposiciones solares veraniegos y más aquellos que están siempre a plena exposición solar sin posibilidad de tapado alguno. Estos acopios al final se encuentran día tras día con aporte calorífico que hace que nunca bajen su temperatura en acopio con todo lo que ello significa, reflejando que el mayor porcentaje de absorción se produce durante los primeros minutos, lo que, en términos prácticos, podría explicar la poca trabajabilidad y pérdida de trabajabilidad en el hormigón-concreto bajo condiciones de alta temperatura. La fricción interna de los agregados (medida mediante los ángulos de reposo y rozamiento interno en arenas) es menor a mayor temperatura; en este caso los valores de estos ángulos serán mayores para arenas con mayor módulo de finura. En definitiva, el agregado es uno de los factores más importantes desde este punto de vista, no sólo por las características específicas de su comportamiento con la temperatura, sino también, porque es el componente de mayor proporción en el hormigón-concreto.
Los ángulos de reposo de los agregados en los acopios decrecen en función de la temperatura; en este caso, los valores de la arena más fina son mayores. Las curvas de comportamiento embargo, estas son muy tenues, sin embargo, desde un punto de vista de tendencias, estos resultados confirman que la fricción interna de los agregados varía con la temperatura, aunque de manera casi imperceptible.
La fricción interna de los agregados (medida mediante los ángulos de reposo y rozamiento interno en arenas) es menor a mayor temperatura; en este caso los valores de estos ángulos serán mayores para arenas con mayor módulo de finura.
Por último, si reparamos en ambientes continentales con temperaturas más suaves a primeras horas de la mañana que aumentan progresivamente durante el día a temperaturas altas, nos encontraremos que el nivel de aumento de la absorción es más drástico pasando de un 5,56% a un 34%, lo que quiere decir que a lo largo del suministro del día nos encontraremos que aportar mayor cantidad de agua nominal a la receta para obtener la misma consistencia, a esto habrá que sumar los materiales lavados que en acopio estén húmedos y vayan secando en el mismo.
En nuestra experiencia todos los detalles son claves y no podemos descuidar ningún punto ya que la suma de todos ni siquiera nos asegura éxito en el diseño de un buen hormigón en condiciones altamente desfavorables. A lo largo de dos décadas hemos ido recogiendo 9 puntos claves para mejorar nuestras opciones de trabajo en las condiciones comentadas que disponemos a continuación:
Temperaturas/Entornos calientes | Temperaturas/Entornos fría/os | ||||||
1 | *Realizar un correcto diseño utilizando todo el conocimiento y los recursos disponibles para un desempeño idóneo. | ||||||
2 | *Utilizar cementos con bajo calor de hidratación lentos y compatibles, o bajar las cantidades kg/m3 que nos ayuden a ralentizar el proceso del inicio de fraguado. | 2 | *Utilizar cementos con alto calor de hidratación rápidos o aumentar las cantidades kg/m3 que nos ayuden a acelerar el proceso del inicio de fraguado. | ||||
3 | *Tapar y/o proteger los acopios de la exposición solar | 3 | *Tapar y/o proteger los acopios de las heladas, nevadas o lluvias | ||||
4 | *Utilizar agua fría, sistemas de hielo, vapor agua helado, acción altamente improbable por la imposibilidad de incluir en las instalaciones de las plantas de hormigón, debido a la tecnología, el alto coste de los sistemas y por supuesto el energético. *Refrigerar los entramados metálicos de los camiones en la medida de lo posible. *Comenzar el suministro en horarios nocturnos o de madrugadas acabando antes de la plena exposición solar y fotoradiación del mediodía. | 4 | *Utilizar agua caliente y/o calentar los materiales con la alta posibilidad de que las instalaciones de las plantas de hormigón no puedan hacerlo debido a la tecnología, el alto coste de los sistemas y por supuesto el energético. | ||||
5 | *Utilizar sinergias de aditivación con efecto retardante (aditivos únicos o en sinergia) | 5 | *Utilizar sinergias de aditivación con efecto acelerante (aditivos únicos o en sinergia) | ||||
Ventajas | Inconvenientes | Ventajas | Inconvenientes | ||||
*Los aditivos retardantes disminuyen la velocidad de hidratación del hormigón-concreto recién colocado y extienden el período durante el cual sigue siendo viable. *Se pueden usar en climas cálidos para tiempos de transporte más largos o para prevenir la formación de juntas frías. *El aumento del tiempo de fraguado de una mezcla puede aumentar el riesgo de agrietamiento debido a que el proceso de aplanado talochado no puede comenzar antes de que ocurra un encogimiento excesivo. | *Retardar los aditivos no evitará la pérdida de trabajabilidad debido a la pérdida de humedad a través de la evaporación de la superficie. *Los aditivos retardantes afectan la tasa de ganancia de resistencia inicial por tan solo 1 ó 2 días, o incluso hasta 7 días, según la dosis. *Necesidad de ajuste concreto de los tiempos de inicio y final del inicio de fraguado (inicial y final) *Algunos aditivos con efectos retardantes debido a su naturaleza o a su baja dosificación generan falta de dispersión en la masa generando en obra los efectos indeseados de “Islas de Fraguado”. *Posibilidad de efecto colchón en la superficie del hormigón generado por un retraso de fraguado en la masa y una desecación rápida de la superficie. *Necesidad de contar con varias instalaciones dosificadoras con todos los inconvenientes que ello conlleva. *Alta precaución de la utilización de expansores ya que generarán altas expansiones desde el inicio de fraguado, acción altamente perjudicial en hormigones-concretos con altas temperaturas en los que buscamos mitigar las mismas. | *Aceleran el tiempo de fraguado, la evolución del calor y el desarrollo de la resistencia inicial. *Aditivos aptos con precaución para reparaciones que necesiten rapidez de acabado. *Aditivos aptos para conseguir resistencias altas iniciales por necesidad de producción. *Generan generalmente etapas de fraguado homogéneas en ambientes internos. *Conseguimiento de altas resistencias iniciales. *Producciones continuas y homogéneas en temperaturas frías. | *Pueden llegar a ser una medida insuficiente. *Por las naturalezas y altas densidades de estos aditivos requieren una homogeneización constante con bombas o sistemas de recirculación o agitación en los acopios que eviten decantaciones *Necesidad de contar con varias instalaciones dosificadoras con todos los inconvenientes que ello conlleva. *En ambientes exteriores con exposición solar continua pueden ocasionar etapas de fraguado rápidas y súbitas. *Existe la posibilidad de tener que utilizar aditivos anticongelantes extras ante temperaturas o heladas que puedan perjudicar al hormigón. *Alta precaución de la utilización de inhibidores de la retracción que suelen pacificar y retardar el inicio de fraguado, modificando las fuerzas capilares de la solución de poro, acción altamente perjudicial en hormigones con bajas temperaturas en los que buscamos mitigar las mismas. | ||||
6 | *Utilizar sistemas de riego continuo sobre los acopios a fin de bajar la temperatura en los mismos. | 6 | *Se recomienda utilizar adiciones calizas(fillers) que suelen acelerar el inicio de fraguado. | ||||
7 | *Regar continuamente el exterior de los bombos de las cubas hormigoneras con el fin de mitigar las altas temperaturas que sin duda afectarán al hormigón. | 7 | *Si podemos contar con agua caliente se pueden regar tras la carga de los camiones el exterior de los bombos de las cubas hormigoneras con el fin de mitigar las bajas temperaturas que sin duda afectarán al hormigón. | ||||
8 | *Realizar hormigonados en horarios nocturnos o de madrugadas sin plena exposición solar buscando los momentos en los cuales las temperaturas no afectarán tanto como a lo largo del día con plena exposición solar. *En obras de interior con altas temperaturas se pueden utilizar sistemas de refrigeración ambiental. | 8 | *Realizar hormigonados solo en horarios diurnos o en su caso con el entorno climatizado con cañones de aire caliente que ayuden a aclimatar la zona y subir las gélidas temperaturas. | ||||
9 | *Durante el transporte del hormigón buscar que los bombos de las cubas estén siempre en movimiento con el fin de que el hormigón vaya suelto, dispersando la aditivación y su efecto evitando que se acelere el inicio de fraguado. |
Si la planta de hormigón-concreto no está situada junto a la obra se puede perder o ganar bastante calor en el transporte a obra, siendo la cantidad perdida o ganada variable de acuerdo con el medio de transporte que se emplee y con las precauciones que se tomen.
Las ruedas de camiones hormigonera que recorran distancias mayores a 10 km son, quizá, por la agitación y el movimiento constante del hormigón-concreto, los más afectados.
Se estima que en un camión hormigonera el descenso de temperatura por hora de transporte esta dado por la siguiente fórmula:
Caso Temperatura fría | Temperatura caliente |
t = 0.25 (tr – ta ) | |
t = Caída o aumento de temperatura esperada durante la entrega. tr = Temperatura requerida en obra para el hormigón ta = Temperatura ambiente Todas ellas expresadas en °C. | |
Así, si un camión hormigonera que tarda una hora en el transporte hasta el vertido, y se requiere un hormigón a 10°C, siendo la temperatura ambiente de -2 °C. La caída de temperatura será: t = 0.25 (10+2)=3ºC=13ºC temperatura de salida significa que perderemos 3ºC en el transcurso del transporte y que necesitaremos que el hormigón salga de la central por lo menos, a 13°C. | Así, si un camión hormigonera que tarda una hora en el transporte hasta el vertido, y se requiere un hormigón a 30°C, siendo la temperatura ambiente de 28ºC. La caída de temperatura será: t = 0.25 (30-28)=0,5ºC=28,5ºC significa que ganaremos 0,5ºC en el transcurso del transporte y que necesitaremos que el hormigón salga de la central por lo menos, a 28,5°C. |
7.Consejos finales sobre la aditivación química para pavimentos de hormigón
Simplemente usted debe saber que la química es necesaria, la química ayuda y toda la industria quiímica diseña y aporta soluciones a los hormigones-concretos que funcionan.
Lo que no funciona es utilizar aditivos genéricos para hormigones estructurales con niveles reológicos diferentes y que una vez vertidos y vibrados permanecen en reposo, mientras que en un pavimento las exigencias productivas son diferentes y la superficie de dichos hormigones-concretos en estado aún fresco debe trabajarse, densificarse y abrir-cerrar poro en fases productivas paulatinas para conseguir acabados compactos y de altas prestaciones.
Teniendo en cuenta esta primera premisa resumimos lo expuesto en este artículo:
- Los aditivos escogidos pueden aportar o perjudicar la reología de la masa de hormigón-concreto. Estudie y escoja los más apropiados para caso, teniendo en cuenta que la decisión se basará en múltiples factores que afectarán al proceso productivo del pavimento.
- Usted debe conocer las tipologías, características, usos, bondades y defectos de cada aditivo y para ello los requerimientos exigibles a esos aditivos en correlacción a lo que de ellos se espera en el desempeño final de la masa de hormigón-concreto, no les pida lo que no puedan dar y exiga que le den lo que están diseñados para dar.
- Recuerde que las condiciones exógenas medioambientales y los calores de hidratación afectarán directamente a la respuesta de las sinergías químicas.
- Si usted es profano del mundo de la química del hormigón-concreto y de las soluciones químicas por favor póngase en manos de un comprobado experto que le ayude en el diseño y puesta de la producción del hormigón-concreto. Toda mala elección perjudicará o echará a perder su futuro pavimento o el de su cliente.
Compartir conocimiento desde Betonia

Este conocimiento que aquí compartimos es parte del Programa hacía el conocimiento activo y la industria de la construcción 4.0 que hemos iniciado hace una serie de años con varias series de actividades formativas, ponencias, jornadas técnicas-prácticas, publicaciones, proyectos etc. trasladando parte de nuestro conocimiento con el fin de singularizar, dignificar, reconocer y destacar los pavimentos de hormigón como unidad específica dentro del mundo de la construcción industrializada.
Nos ha costado mucho esfuerzo, tiempo y multitud de errores solventados, siempre con método empírico, para llegar a disponer de esta experiencia que ahora compartimos, siendo conscientes de que no es más que una pequeña parte del «verdadero conocimiento».
Aquellos que deseen copiar, usurpar o adquirir sin merecimiento deber tener claro que los conocimientos ‘se adquieren, se trabajan y se perfeccionan de manera propia mediante mucho trabajo, vencer barreras y superarse cada día.
Óscar Candás(Betonia Products)
Febrero 2024