Editorial Note: We are an inventory management software provider. While some of our blog posts may highlight features of our own product, we strive to provide unbiased and informative content that benefits all readers.
Perishable goods are products that have a limited shelf life and can spoil or deteriorate quickly if not stored properly.
These products may include fresh fruits and vegetables, dairy products, meats, seafood, baked goods, and other similar items. The quality and safety of perishable goods can be compromised if they are not handled and stored correctly, and as a result, they must be managed carefully to avoid spoilage and waste.
Time-sensitive products, on the other hand, are products that have a limited timeframe for delivery or use. These products may include medications, vaccines, blood products, and other healthcare-related items that must be delivered to their destination quickly and within a specific timeframe to ensure their effectiveness.
Time-sensitive products may also include goods that are in high demand during certain seasons, such as holiday gifts, seasonal foods, and other similar items. Effective inventory management is crucial for time-sensitive products to ensure that they are delivered to their destination on time and in good condition.
Table of Contents
- Importance of Effective Inventory Management
- Overview of the Article’s Main Points
- Setting Appropriate Inventory Levels
- Using First-In, First-Out (FIFO) Inventory System
- Monitoring Expiration Dates
- Implementing a Robust Quality Control System
- Using Data Analytics to Forecast Demand
- Working Closely With Suppliers
- Using Appropriate Storage and Transportation Methods
- Conclusion
Importance of Effective Inventory Management for Such Products:
Effective inventory management for perishable goods and time-sensitive products is essential for several reasons:
1. Maximizing Product Quality:
Perishable goods and time-sensitive products have a limited shelf life or a specific timeframe for use or delivery. Effective inventory management ensures that these products are stored, handled, and delivered correctly, maximizing their quality and freshness.
2. Minimizing Waste:
Perishable goods and time-sensitive products that are not managed properly can spoil, deteriorate, or expire, resulting in waste and financial loss. Effective inventory management can minimize waste by ensuring that products are used or sold before they expire or lose their quality.
3. Meeting Customer Demand:
Perishable goods and time-sensitive products are often in high demand, and failure to meet customer demand can lead to lost sales and reputational damage. Effective inventory management ensures that adequate inventory levels are maintained to meet customer demand.
4. Maintaining Regulatory Compliance:
Many perishable goods and time-sensitive products are subject to regulatory requirements, such as temperature control, labeling, and expiration date tracking. Effective inventory management ensures compliance with these regulations and reduces the risk of penalties or fines.
5. Improving Supply Chain Efficiency:
Effective inventory management can improve supply chain efficiency by reducing lead times, minimizing stockouts, and optimizing inventory levels. This can help to reduce costs and improve overall business performance.
Effective inventory management is crucial for maximizing product quality, minimizing waste, meeting customer demand, maintaining regulatory compliance, and improving supply chain efficiency for perishable goods and time-sensitive products.
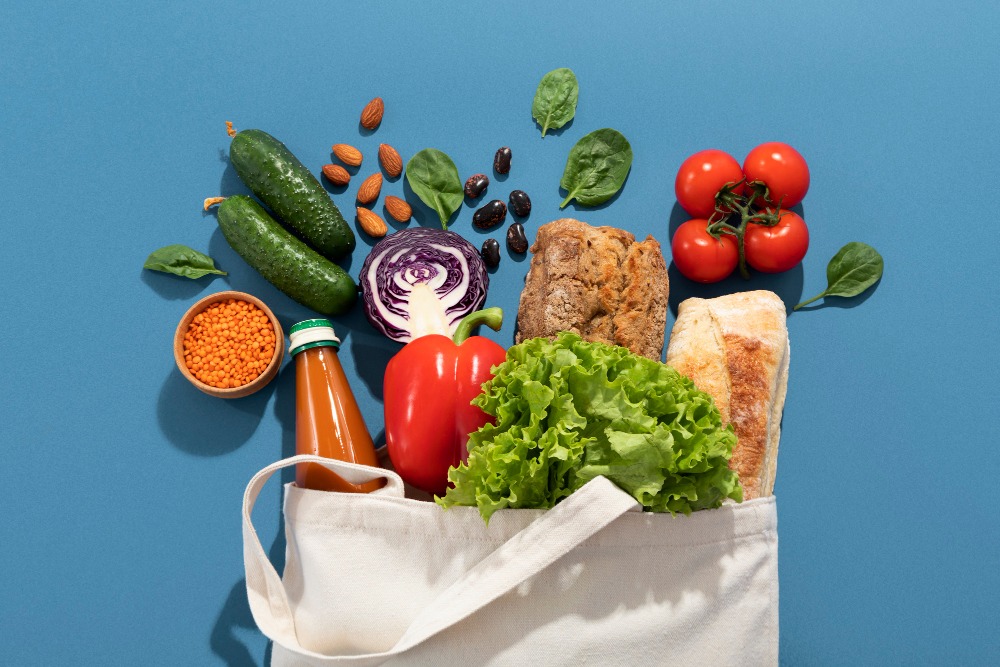
Overview of the Article’s Main Points:
This article will explore the topic of inventory management for perishable goods and time-sensitive products.
The main points covered in the article are:
- Setting appropriate inventory levels: Explanation of how to determine appropriate inventory levels for perishable goods and time-sensitive products, and strategies for avoiding overstocking and stockouts.
- Using first-in, first-out (FIFO) inventory system: Explanation of the FIFO system and its benefits for perishable goods and time-sensitive products, along with examples of how to implement a FIFO system.
- Monitoring expiration dates: Explanation of the importance of tracking expiration dates, the risks of not monitoring expiration dates, and strategies for tracking expiration dates effectively.
- Implementing a robust quality control system: Explanation of the importance of quality control for perishable goods and time-sensitive products, examples of quality control measures, and the benefits of effective quality control.
- Using data analytics to forecast demand: Explanation of how data analytics can be used to forecast demand for perishable goods and time-sensitive products, the benefits of forecasting demand, and strategies for effective demand forecasting.
- Working closely with suppliers: Explanation of the importance of supplier relationships for inventory management, strategies for building and maintaining good relationships with suppliers, and benefits of good supplier relationships.
- Using appropriate storage and transportation methods: Explanation of the importance of proper storage and transportation for perishable goods and time-sensitive products, strategies for proper storage and transportation, and examples of temperature-controlled storage and transportation.
The article will conclude with a recap of the main points and an emphasis on the importance of effective inventory management for perishable goods and time-sensitive products, along with final thoughts and recommendations.
Setting Appropriate Inventory Levels:
Setting appropriate inventory levels for perishable goods and time-sensitive products is crucial for effective inventory management.
Here are some strategies for setting appropriate inventory levels:
1. Analyze Historical Sales Data:
Analyzing historical sales data can help to identify patterns in demand and forecast future demand. This information can be used to set appropriate inventory levels and avoid overstocking or stockouts.
2. Consider Lead Times:
Lead times for ordering and restocking perishable goods and time-sensitive products can vary. It is essential to factor in these lead times when setting inventory levels to ensure that there is enough stock to meet demand during the lead time.
3. Consider Expiration Dates:
Perishable goods and time-sensitive products have limited shelf lives, and it is crucial to factor in expiration dates when setting inventory levels. The goal is to avoid overstocking to minimize waste and stockouts to meet customer demand.
4. Utilize Safety Stock:
Safety stock is an additional inventory buffer that can be used to cover unexpected increases in demand, delays in restocking, or unexpected spoilage. It is important to determine the appropriate level of safety stock to maintain adequate inventory levels while minimizing waste.
5. Continuously Monitor Inventory Levels:
Continuously monitoring inventory levels can help to identify trends, track demand patterns, and adjust inventory levels accordingly. Regular monitoring can help to avoid overstocking or stockouts and maintain appropriate inventory levels.
By setting appropriate inventory levels for perishable goods and time-sensitive products, businesses can avoid waste, meet customer demand, and improve supply chain efficiency. It is essential to regularly review and adjust inventory levels to ensure that they are appropriate for current demand patterns and lead times.
Using First-In, First-Out (FIFO) Inventory System:
The first-in, first-out (FIFO) inventory system is a popular method for managing perishable goods and time-sensitive products. This method involves using the oldest inventory first, to ensure that products are sold or used before they expire or deteriorate.
Here are some benefits of using a FIFO inventory system:
- Reduces waste: By using the oldest inventory first, a FIFO system ensures that perishable goods and time-sensitive products are sold or used before they expire or deteriorate. This helps to minimize waste and financial loss.
- Improves product quality: Using the oldest inventory first ensures that the freshest products are used or sold first, maximizing product quality and customer satisfaction.
- Simplifies inventory management: FIFO is a straightforward inventory management system that is easy to understand and implement. It does not require complex inventory tracking systems or extensive record-keeping.
- Minimizes stock obsolescence: Using a FIFO system helps to minimize the risk of stock obsolescence by ensuring that older inventory is used or sold before new inventory is added to the stock.
To implement a FIFO system, it is necessary to have a clear understanding of the inventory’s expiration dates and shelf lives. Perishable goods and time-sensitive products should be properly labeled with expiration dates and arranged in a way that ensures that the oldest inventory is used or sold first. FIFO can be implemented manually, but many businesses also use inventory management software to automate the process.
A FIFO inventory system can help to reduce waste, improve product quality, simplify inventory management, and minimize stock obsolescence. It is a popular method for managing perishable goods and time-sensitive products and is well-suited for businesses that prioritize product quality and customer satisfaction.
Monitoring Expiration Dates:
Monitoring expiration dates is critical for effective inventory management of perishable goods and time-sensitive products.
Here are some strategies for monitoring expiration dates:
- Establish a system for tracking expiration dates: It is essential to establish a system for tracking expiration dates, whether through manual record-keeping or inventory management software. This system should be regularly monitored to ensure that products are used or sold before they expire.
- Train staff on expiration dates: All staff members involved in handling perishable goods and time-sensitive products should be trained on the importance of monitoring expiration dates and how to identify expired products.
- Conduct regular inventory checks: Regular inventory checks can help to identify expired products and prevent them from being used or sold. These checks should be conducted at regular intervals, and expired products should be removed from inventory immediately.
- Rotate inventory regularly: Rotating inventory regularly can help to ensure that the oldest inventory is used or sold first. This can be achieved through a FIFO inventory system or by regularly checking expiration dates and using or selling products before they expire.
- Consider the effects of temperature and storage conditions: Temperature and storage conditions can impact the shelf life of perishable goods and time-sensitive products. It is essential to consider these factors when monitoring expiration dates and storing products.
By effectively monitoring expiration dates, businesses can ensure that their perishable goods and time-sensitive products are used or sold before they expire. This can help to minimize waste, improve product quality, and reduce the risk of spoilage.
Implementing a Robust Quality Control System:
Implementing a robust quality control system is critical for ensuring that perishable goods and time-sensitive products meet customer expectations and comply with regulatory requirements.
Here are some strategies for implementing a robust quality control system:
- Establish clear quality standards: Clear quality standards should be established for each product, including specifications for appearance, taste, texture, and odor. These standards should be communicated to all staff members involved in handling and processing the products.
- Conduct regular product testing: Regular product testing can help to identify any issues with quality and ensure that products meet established quality standards. Testing can include sensory analysis, microbiological testing, and chemical analysis, depending on the product.
- Train staff on quality control procedures: All staff members involved in handling and processing perishable goods and time-sensitive products should be trained on quality control procedures, including how to identify and address quality issues.
- Implement corrective actions: If quality issues are identified, corrective actions should be implemented to prevent further issues from occurring. This can include adjusting processing methods, improving storage conditions, or changing suppliers.
- Continuously monitor and improve quality control procedures: Quality control procedures should be regularly reviewed and updated to ensure that they are effective and up to date. This can include implementing new testing methods, improving staff training, or updating quality standards.
A quality control system for perishable goods is essential for businesses to meet customer expectations and comply with regulations. It can also help to improve customer satisfaction, reduce waste and costs, and build a strong brand reputation.
Using Data Analytics to Forecast Demand:
Using data analytics to forecast demand is an effective strategy for managing inventory of perishable goods and time-sensitive products.
Here are some strategies for using data analytics to forecast demand:
- Gather relevant data: Relevant data for forecasting demand can include sales history, seasonality, customer demographics, marketing campaigns, and external factors like weather and holidays. This data can be gathered through various sources, including point-of-sale systems, customer surveys, and social media.
- Analyze data using forecasting techniques: Data can be analyzed using various forecasting techniques, including time series analysis, regression analysis, and machine learning algorithms. These techniques can help to identify patterns, trends, and seasonality in the data, and predict future demand.
- Implement inventory optimization models: Once demand is forecasted, inventory optimization models can be used to determine the optimal inventory levels and reorder points. These models can factor in lead times, service levels, and holding costs to determine the most cost-effective inventory levels.
- Monitor and adjust forecasts: Forecasts should be regularly monitored and adjusted based on actual sales data. This can help to improve the accuracy of the forecasts and ensure that inventory levels remain optimal.
By using data analytics to forecast demand, businesses can make more informed inventory management decisions and improve their bottom line. Data analytics can help businesses to reduce inventory costs, prevent stockouts, and improve customer satisfaction.
Working Closely With Suppliers:
Working closely with suppliers is an essential component of effective inventory management for perishable goods and time-sensitive products.
Here are some strategies for working closely with suppliers:
- Establish clear communication channels: Clear communication channels should be established with suppliers to ensure that both parties are aware of inventory needs, lead times, and quality requirements. This can include regular meetings, email communication, or phone calls.
- Develop strong relationships: Developing strong relationships with suppliers can help to improve collaboration and communication. This can be achieved through regular communication, face-to-face meetings, and building a rapport with supplier contacts.
- Share data and forecasts: Sharing sales data and demand forecasts with suppliers can help them to plan production and adjust their inventory levels accordingly. This can improve supplier responsiveness and help to prevent stockouts or overstocking.
- Establish quality control measures: Quality control measures should be established with suppliers to ensure that products meet established quality standards. This can include regular product testing, supplier audits, and implementing corrective actions if quality issues arise.
- Negotiate favorable terms: Negotiating favorable terms with suppliers can help to reduce costs and improve supply chain efficiency. This can include negotiating bulk discounts, optimizing delivery schedules, and establishing flexible payment terms.
Working closely with suppliers is essential for effective inventory management of perishable goods and time-sensitive products. By establishing clear communication channels, developing strong relationships, sharing data and forecasts, establishing quality control measures, and negotiating favorable terms, businesses can improve supply chain efficiency, reduce costs, and ensure that they have the right inventory levels to meet customer demand.
Using Appropriate Storage and Transportation Methods:
Using appropriate storage and transportation methods is critical for maintaining the quality and safety of perishable goods and time-sensitive products.
Here are some strategies for using appropriate storage and transportation methods:
- Choose the appropriate storage and transportation methods: Choosing the appropriate storage and transportation methods can depend on the type of product, its temperature requirements, and the distance and duration of transportation. This can include refrigerated trucks, cold storage facilities, or temperature-controlled shipping containers.
- Monitor storage and transportation conditions: Storage and transportation conditions should be monitored regularly to ensure that products are being stored and transported within the appropriate temperature range. This can include using temperature monitoring devices, regular inspections, and tracking shipment status.
- Implement contingency plans: Contingency plans should be established in case of unexpected events that can impact storage and transportation conditions. This can include backup power sources, alternative routes, and emergency storage options.
- Train staff on proper handling procedures: All staff members involved in handling and transporting perishable goods and time-sensitive products should be trained on proper handling procedures to ensure that products are not damaged or contaminated during transportation.
- Implement quality control measures: Quality control measures should be established to ensure that products are being stored and transported in compliance with established quality standards. This can include regular testing, supplier audits, and implementing corrective actions if quality issues arise.
Using appropriate storage and transportation methods is essential for maintaining the quality and safety of perishable goods and time-sensitive products. By implementing the following strategies, businesses can reduce the risk of spoilage, contamination, or damage:
Conclusion:
Effective inventory management for perishable goods and time-sensitive products is critical to meet customer demand, reduce waste and spoilage, and ensure product quality and safety.
Businesses can implement various strategies, including setting appropriate inventory levels, using the first-in, first-out (FIFO) inventory system, monitoring expiration dates, implementing a robust quality control system, using data analytics to forecast demand, working closely with suppliers, and using appropriate storage and transportation methods.
By implementing these strategies, businesses can improve supply chain efficiency, reduce costs, and maintain product quality and safety. Effective inventory management is a continuous process that requires regular monitoring, evaluation, and improvement to ensure that businesses are meeting their inventory goals and objectives
Take a Quiz Test - Test Your Skill
Test your inventory management knowledge. Short multiple-choice tests, you may evaluate your comprehension of Inventory Management.