Elton Voltolini, Dr. Eng
Capacidade Produtiva - base para o resultado dos negócios
Planejamento e Gestão da Capacidade como base para atender demanda de forma eficiente
Conhecer a fundo a capacidade de produção da empresa é fundamental para garantir um bom atendimento ao mercado com desempenho financeiro adequado do negócio. Trata-se de informação basilar para que gestores possam entender o potencial de geração de valor da empresa e possuem horizontes de tomada de decisão de curto, médio e longo prazos.
Neste artigo iremos discorrer sobre o conceito de capacidade produtiva e sobre o processo para definição da mesma. Também serão discutidos os benefícios a cerca do conhecimento da capacidade produtiva para as organizações de forma geral e então, apresentados e explicados os tipos de capacidade e ade produtiva para organizações de forma geral. Adicionalmente abordaremos os índices que permitem compreender a relação entre os tipos de capacidade, trazendo com isso uma visão geral sobre como aumentar a capacidade de produção.
O Conceito de Capacidade de Produção
Para gerenciar e planejar as operações, quer seja de uma tecelagem, de um restaurante, de um hotel ou de um supermercado, é necessário ter domínio sobre os limites de atendimento à demanda em determinadas condições. Quantos hóspedes podemos receber simultaneamente? Conseguiremos atender o pedido da montadora X para o próximo trimestre? Quantos pedidos podemos separar diariamente? Quantos clientes conseguimos atender no caixa por hora aos sábados à noite? Estas são perguntas típicas em diversos contextos diferentes, mas cujas respostas interessam a diversos setores das organizações, tais como: Comercial, Produção, Logística, Financeiro, PCP (Planejamento e Controle de Produção). Em todos os casos, busca-se saber qual a capacidade de produção, ou das operações.
A capacidade de produção está associada a quantidade máxima de processamento de bens e serviços que um sistema de transformação é capaz de entregar dentro de determinadas condições de normalidade. É importante salientar que por sistema de transformação podem ser entendidos: unidade fabris, centros de distribuição, hospitais, lojas, terminais portuários, restaurantes, dentre outros. Em caráter micro, a preocupação com a capacidade de produção também se estende a uma máquina, centro de trabalho, operador, porém sua aplicação é obviamente mais restrita do que a gestão e planejamento de capacidade de um sistema de transformação com os já aqui citados.
O nível de capacidade fica determinado pelos recursos de transformação de que o sistema dispõe para desempenhar suas atividades, ou seja, trata-se de uma combinação de pessoas, equipamentos, instalações, tecnologias e estruturas. Engana-se, contudo, aquele que apenas considera os aspectos quantitativos destes recursos, que apesar de serem importantes, não são os únicos aspectos a serem considerados destes recursos. A qualificação/ especificações dos recursos são tão ou mais importantes que o aspecto quantitativo. Sob uma perspectiva mais integrada do sistema de transformação, ou mesmo da organização como um todo, não é desprezível o papel desempenhado na articulação dos recursos transformadores, trazendo uma visão mais horizontal de processos e fluxos aliados a tomada de decisão em diferentes horizontes de planejamento de capacidade.
Ao trazer exemplos de questões que remetem ao conceito de capacidade de produção deve chamar atenção o fato de que se pode evidenciar um caráter dinâmico, ou temporal da capacidade, assim como um caráter estático, ou de escala. A capacidade dinâmica trás o olhar sobre o movimento, sobre a agregação de valor, sobre um fluxo temporal e pode ser percebida em métricas como: pedidos separados, clientes atendidos por hora, peças produzidas, por exemplo. A capacidade estática - muito útil para operações de logística de armazenagem - trazem o olhar de volumetria e escala em um momento, podendo ser expressa em métricas como: número de posições porta-palete do armazém, quantidade de containers transportados por um navio, número de quartos de um hotel, número de assentos de uma avião.
A gestão da capacidade apesar de ser uma prática difundida em especial no ambiente industrial está longe de algo trivial na maioria dos contextos. Pelo fato de buscar o melhor equilíbrio para o dimensionamento de recursos (investimentos em instalações, equipamentos, pessoas, etc.) com o comportamento da demanda (variabilidade, sazonalidade, expectativas dos clientes), a margem de erro aumenta com a maior granularidade da análise e quanto maior o horizonte de temporal . Com base nisso, é possível que a organização experimente períodos de ociosidade em alguns ou todos os seus recursos e períodos de falta de capacidade de atendimento gerando insatisfação dos clientes, má percepção sobre a qualidade de seu serviço, vendas perdidas, etc.
A identificação de momentos de ociosidade e de falta de capacidade também devem ser analisados sob diferentes níveis de amplitude, ou seja, da rede, da instalação, do setor e do centro de trabalho. Dificilmente teremos fluxos tão cadenciados e regulares neste diversos níveis a ponto de que todas as partes das redes ou das organizações operem simultaneamente no mesmo nível de utilização de suas capacidades. Com base nesta constatação, o conceito de "gargalo" oriundo da Teoria das Restrições é aplicável. Dependendo da natureza da demanda, o uso de diferentes partes de uma operação pode atingir sua capacidade máxima e atuar como restrição para o nível superior de amplitude. Por exemplo, um restaurante pode ter uma boa cadência de retirada dos pedidos, preparação dos alimentos e da disponibilização dos pedidos, mas gerar filas para fechar a conta, por quê o responsável também recebe pedidos do serviço de tele entrega.
Adicionalmente, não se devem subestimar os fatores que afetam a execução das operações no dia-a-dia e que contribuem para que as entregas dos sistema de produção se distanciem ainda mais do planejado, trazendo por vezes fortes questionamentos sobre a real capacidade de execução e entrega. Na próxima seção serão abordados os impactos do adequado domínio da gestão e do planejamento da capacidade produtiva nas empresas de forma geral e nos seus departamentos.
Importância do Planejamento e Gerenciamento da Capacidade Produtiva
O acompanhamento ativo da capacidade de produção, o gerenciamento e o planejamento eficaz de alterações em sua capacidade de produção trazem diversos benefícios para sua empresa e está diretamente relacionado ao planejamento agregado de produção, especialmente em se tratando de processos de empresas industriais. Num escopo mais abrangente de operações de transformação em serviços e comercio, bem como das atividades logísticas, o fluxo de planejamento possui características particulares. No entanto, cabe dizer que em todos os casos objetiva-se não apenas a maximização da utilização dos recursos disponíveis, mas também o aumento da eficiência de suas operações.
De uma forma geral, o planejamento e gerenciamento da capacidade (PGC) permite aumentar a produção quando necessário, minimizando o risco de excesso de estoque. Tudo isso junto reduzirá os custos, permitindo à organização ter capacidade de responder aos picos de demanda. No âmbito dos serviços, a forma como a capacidade é gerenciada é ainda mais crítica e pode determinar se um negócio é rentável ou não, pois tem impacto nos investimentos e nos custos operacionais. Dadas certas características dos serviços, a capacidade é perecível, não pode ser estocada (estocabilidade), tal como acontece com quarto de hotel não ocupado ao final de uma diária, de um dia sem projeto de um consultor, de uma consulta agendada sem o comparecimento do paciente. Em todos os casos anteriores, não é possível "estocar" horas e recursos ociosos para um outro dia em que o número de solicitações de serviço supere sua capacidade de atendimento, portanto, da criticidade ainda maior no contexto dos serviços.
Conforme já foi escrito, dado que a capacidade produtiva e seu planejamento influenciam na lucratividade e eficiência da produção, portanto, métricas bastante amplas e relevantes das empresas; diversos aspectos de desenvolvimento da empresa são afetados pelas decisões tomadas pelos gestores, quanto à capacidade e seu planejamento. Sendo eles: custos de produção, receitas, capital de giro, qualidade dos bens ou serviços, velocidade de resposta à demanda do cliente, confiabilidade do fornecimento e flexibilidade de atendimento à demanda (SLACK; CHAMBERS; JOHNSTON, 2009).
O planejamento e gerenciamento da capacidade (PGC) possui impactos em diversos aspectos de desempenho, os quais estão abaixo relacionados de forma sintética:
melhora da assertividade de gestores e colaboradores nas diversas áreas de negócio;
redução dos custos pelo equilíbrio entre capacidade e demanda. Sem utilização excessiva ou subutilização da capacidade;
maximização do atendimento da demanda reduzindo a perdas de receita;
manutenção dos níveis de estoques otimizados (para bens), liberando capital de giro;
incremento da qualidade de produtos e serviços e reduzir a probabilidade de ocorrência de erros;
aumento da velocidade de resposta à demanda do cliente, seja pela geração de pequenos estoques, seja pela acertada previsão da demanda;
maior flexibilidade para responder a aumentos inesperados na demanda;
maior responsividade às demandas do mercado, encurtando o prazo de atendimento;
aumento da previsibilidade da entrega e a acurácia do Available-to-Promise (ATP);
melhora da rotina e a produtividade dos colaboradores, pela estabilização e maior previsibilidade de sua jornada de trabalho;
melhora utilização dos recursos materiais e dos insumos, evitando custos extras por uso emergencial;
alinhamento entre comercial, financeiro, produção, logística e compras para atender as demandas planejadas e priorizadas entre estes departamentos. Fruto deste, é possível observar melhor relacionamento interdepartamental;
maior assertividade na definição das metas comerciais, de produção e de entrega.
Os impactos - como se percebe - são realmente amplos, justificando o esforço do planejamento e da gestão da capacidade para efeito de ação gerencial, mas também de planejamento e orçamentação. Conhecer capacidade produtiva do sistema permite à própria equipe entender melhor o próprio negócio e assim atender melhor seus clientes. Além disso, é possível identificar gargalos e com base nisso, orientar iniciativas de melhoria com intuito de elevar a capacidade produtiva da empresa.
Processo de planejamento e gerenciamento da capacidade produtiva
A capacidade de produção diz respeito ao número máximo de unidades de produção que uma organização é capaz de fazer com seus recursos disponíveis, tais como máquinas e mão-de-obra produtiva. Desse modo, ao realizar as projeções financeiras para uma empresa deve-se garantir que ela terá capacidade e recursos de produção suficientes para fabricar os produtos necessários para atender a previsão de vendas e, por consequência, dispor dos níveis adequados de estoques e de recursos transformadores.
O planejamento da capacidade produtiva tem por objetivo, especificar qual nível de capacidade irá atender às demandas de mercado de formar eficiente, em termos de custo. O planejamento da capacidade é segmentado em três espaços temporais: longo (maior que 18 meses), médio (entre 6 a 18 meses), e curto (menos de 6 meses).
No planejamento de capacidade de longo prazo as mudanças nos níveis de capacidade são mais representativos e normalmente envolvem decisões sobre aumento ou redução de ativos, bem como decisões de localização de suas instalações e sobre as principais tecnologias de produção. Neste horizonte, que pode ser também entendido como uma fase do planejamento da capacidade, é tomada a decisão sobre o momento em que deve haver a alteração da capacidade, situando-se entre (SLACK, N.; CHAMBERS, S.; JOHNSTON, R., 2002, ps. 191- 192):
capacidade antecipada à demanda - o aumento da capacidade antecede à demanda efetiva, gerando disponibilidade suficiente para atendimento da demanda;
capacidade acompanha a demanda - o aumento da capacidade é planejado para que o mesmo não exceda a demanda e em alguns momentos esteja abaixo da mesma.
No nível do planejamento e gestão da capacidade as mudanças de capacidade são de menor monta e envolvem custos e riscos menores do que as decisões de longo prazo, tratando do monitoramento da capacidade existente e utilizada, bem como a tomada de decisão e para responder às flutuações da demanda no curto e médio prazos.
Com intuito de esclarecer a sequencia de tomadas de decisão para do PGC, dividimos a mesma em algumas etapas, as quais são abaixo descritas:
Estimar as vendas agregadas - para elaborar planos empresariais a empresa precisa realizar a Previsão de Vendas, pois a mesma define qual será a demanda pelos seus produtos, após confirmar que o produto tem espaço no mercado em termos comerciais. Também nesta etapa devem ser verificadas características de tendência, sazonalidade das vendas e investigados fatores que produzam efeitos de correlação das vendas. Aqui o olhar está no médio e curto prazos e envolve toda a linha de produtos, assumindo mix constante .
Estimar as vendas para produtos - detalhar a etapa 1, buscando trazer informações sobre mix de vendas dentro dos horizontes de planejamento e para os mercados atendidos.
Calcular a capacidade agregada - avaliar a capacidade existente para determinar suas capacidades efetivas e de projeto , bem como suas taxas atuais de eficiência e utilização (conceitos abordados na próxima seção). Nesta etapa a análise é agregada, envolvendo diversos produtos (bens e serviços) da empresa e com foco nos níveis de rede e de instalações, considerando-se um mix uniforme de produtos. Por este motivo são adotadas unidades de medida que façam sentido para cada "plataforma" de produto, tais como m2, toneladas, m3, procedimentos médicos, refeições, dentre outros. Esta etapa segue o direcionamento do planejamento de longo prazo, que identificou se o movimento futuro requer expansão ou retração de capacidade.
Identificar maneiras de ajustar a capacidade existente - com base na avaliação da necessidade de expansão ou retração no longo prazo, são avaliadas as medição e na compreensão das perdas existentes, busca-se elevar a capacidade se este for o caso. Identificar as políticas alternativas de capacidade, escolhendo entre: políticas de capacidade constante, políticas de acompanhamento da demanda e política gestão da demanda. Cada política é composta de uma séria de abordagens distintas possíveis, que precisam ser consideradas.
Escolher as políticas de capacidade mais adequadas - através de análise de custos e de risco é feita a escolha da política alternativa de capacidade e detalha a sua forma de execução. Compare os benefícios qualitativos para cada alternativa. Se você terceirizasse partes de sua produção, por exemplo, poderia manter os mesmos padrões de qualidade?
Executar políticas e monitorar resultados - etapa de implementação das medidas de ajuste de capacidade de médio e curto prazos, que estão diretamente ligadas à gestão de atendimento (GATE) e a gestão de ordens (GORD). Aqui o acompanhamento de projetos, iniciativas e resultados operacionais é feito.
Importante destacar que existe uma diferença entre prever demanda e realizar a previsão de vendas, sendo abaixo explicados os dois conceitos:
Previsão de Demanda - trata-se de um conceito que deve preceder a previsão de venda, sendo dependente das condições econômicas e de consumo no mercado. Seu objetivo é o de determinar o interesse do consumidor por um produto em todo o mercado. Sem previsão de demanda, o negócio assume o risco de prosseguir e operar em um mercado que potencialmente não precisa de seu produto.
Previsão de Vendas - trata-se de uma projeção feita pela empresa para a quantidade total de receitas que espera auferir em um determinado período futuro. Sua elaboração está posicionada no início do planejamento empresarial, porque é a partir das vendas que são derivadas todas as demais projeções e simulações.
Tipos de Capacidade Produtiva
Para organizações de um produto ou de produtos muito homogêneos o cálculo da capacidade é mais simplificado, pois é possível relacionar diretamente os recursos transformadores dedicados com outputs (saídas) únicas ou homogêneas. O cálculo da capacidade de produção torna-se mais difícil e com maior margem de erro quanto maior a diversidade de outputs e de recursos de transformação. Existem, inclusive os casos onde um bem pode ser fabricado segundo diversos roteiros de fabricação distintos, conforme a análise de ocupação da fábrica, afetando diretamente o tempo de ciclo de produção e a produção horária, fazendo com que a capacidade de produção seja flutuante de acordo com o mix planejado de produção.
É possível inclusive perceber uma relação entre os tipos de arranjos físicos com o grau de dificuldade para o estabelecimento mais preciso das capacidades de produção, justamente pelo fato de que a escolha dos arranjos físicos está associada em grande parte com as características dos sistemas de produção: variedade de output, e volume de output. Conforme a figura 01, a intermitência do fluxo de produção está relacionada à maior variedade de produtos (bens ou serviços), com menor quantidade produzida, exigindo arranjos físicos de características mais flexíveis, com diversas combinações de sequencias de produção.
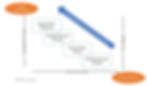
Figura 01 - Relação entre Arranjos Físicos e Complexidade da Determinação da Capacidade
Fonte: EXCENT Consultoria
As características e aplicações de cada um dos arranjos físicos são abordados em outro artigo de nosso Blog, mas vale estabelecer a ponte entre as temáticas de capacidade e de arranjo físico. Desta forma, feitas as considerações iniciais sobre complexidade de calcular a capacidade de produção em determinados contextos, deve-se voltar ao processo de planejamento e gestão da capacidade, que tem em suas etapas a necessidade de realizar os cálculos para a capacidade existente e necessária.
Segundo Watts et al. (2009), a medida da capacidade ajuda a identificar o grau de produção relativa frente a utilização não produtiva. O modo no qual a capacidade produtiva é mensurada e relatada afeta as decisões gerenciais, assim como o desempenho econômico da empresa. O cálculo da capacidade produtiva pode variar dependendo da aplicação dos dados e da filosofia da instituição. Com intuito de esclarecer os tipos de capacidade, os mesmos serão explicados a seguir.
Capacidade Produtiva Instalada
A capacidade instalada de uma companhia representa o nível de produção em relação ao seu potencial máximo produtivo, sem interrupções, desconsiderando perdas, paradas ou outro tipo de problema.
Neste caso, é a capacidade produtiva obtida em uma jornada de trabalho de 24 horas, durante todos os dias do mês, ignorando as paradas para manutenção e perdas decorrentes de erros de programação da produção.
Exemplo: uma fundição tem capacidade de produzir 3,5 toneladas por hora, então sua capacidade instalada = 3,5 toneladas / hora * 24 horas * 30 dias = 3,5 * 24 * 30 = 2.520 toneladas por mês.
Capacidade Produtiva Disponível ou de Projeto
A capacidade produtiva disponível, também conhecida como capacidade de projeto, é similar a anterior, ou seja, não leva em conta paradas, perdas e outros problemas. A diferença é que aqui só deve ser considerado a jornada de trabalho real, isto é, o regime de turnos de trabalho escolhido pela empresa adicionados às horas-extras trabalhadas.
Exemplo: considere uma confecção que produza 330 peças por hora, que opere em um turno de 8,8 horas, durante 5 dias por semana por 4 semanas num mês, então sua capacidade disponível = 330 peças/hora * 1 turno * 8,8 horas * 5 dias * 4 semanas = 330 * 1 * 8,8 * 5 *4 = 58.080,0 peças por mês.
Capacidade Efetiva
A capacidade efetiva demonstra o quanto a organização verdadeiramente é capaz de produzir. Neste caso é considerada a capacidade disponível subtraídas das perdas planejadas dessa capacidade, que são: setups (tempo de preparação), manutenções preventivas, auditorias da qualidade, trocas de turnos, intervalos de operações, produção de amostras dentre outros.
Exemplo: considere que uma empresa produz cadeiras para escritório e nela são trabalhadas 8 horas por dia (ou 460 minutos) - já descontado parada para refeição - e que existam pausas para manutenção preventiva, em 3% desse tempo disponível; se cada cadeira precisa de 35 minutos para ser montada, a capacidade produtiva efetiva = 460 min * (100%-3%) *( 1 peça/ 35 min) = 460 * 0,97 * (1/35) = 12,75 peças por dia.
Revise seu processos de planejamento de operações e reduza desperdícios.
Capacidade Realizada
A capacidade realizada trás o resultado da execução de fato, considerando as saídas (outputs) dos sistema de transformação. Neste tipo de capacidade são adicionalmente consideradas as perdas não previstas em relação à capacidade efetiva, ou seja, aquilo que não estava dimensionado e programado pela equipe de gestão. São exemplos de perdas não previstas: quebra de máquinas e de equipamentos de movimentação, falta de matéria-prima, falta de energia, problemas com operadores, problemas de qualidade etc.
Uma sugestão para fazer esse cálculo é analisar o histórico de perdas não previstas da indústria, dessa forma você terá pelo menos uma ideia da capacidade produtiva realizada. Atualmente as indústrias tem ao seu dispor softwares do tipo MES (Manufacturing Execution System, ou Sistema de Execução da Manufatura)), que permitem o acompanhamento em tempo real das máquinas através da conexão com CLPs (Controladores Lógico Programáveis), assim como os Centros Logísticos já dispõe de aplicações integradas com softwares tipo WMS (Warehouse Management System, ou Sistema de Gerenciamento de Armazéns) para monitorar as atividades executadas e a produtividade de operadores e equipamentos. Com soluções como estas a projeção de horas realizadas torna-se cada vez mais aderente ao realizado e a compreensão sobre as perdas é substancialmente aperfeiçoada.

Figura 02 - Tipos de Capacidade Produtiva
Fonte: EXCENT Consultoria
Na figura 2, trazemos os quatro tipos de capacidade, procurando identificar sua relação de grandeza, além de apresentar a relação com as perdas planejadas e não planejadas. Para melhor entender, confira nosso passo-a-passo:
Conheça a capacidade instalada - o primeiro passo para entender a capacidade produtiva é calcular a capacidade do centro de produção por hora. No caso de máquinas (nossos centros de produção) com a mesma, multiplica-se a capacidade de uma máquina sem nenhum tipo de parada, trabalhando de forma ininterrupta pelo número de máquinas. Evidentemente, trata-se de um cálculo totalmente teórico.
Estabeleça a capacidade disponível por cada produto - o próximo passo parte do cálculo da capacidade de produção para um produto específico, normalmente o produto mais representativo no centro de produção. Neste caso, deve-se primeiramente determinar o tempo padrão de produção para um unidade do produto e então, dividir a capacidade diária (horas) do sistema de transformação como um todo (planta fabril, centro de distribuição, restaurante, hospital, por exemplo) pelo tempo padrão de uma unidade do produto. O tempo padrão é o tempo necessário para executar uma operação de acordo com um método estabelecido, em condições determinadas, por um operador apto e treinado, possuindo uma habilidade média, trabalhando com esforço médio, durante todas as horas do serviço (TOLEDO JUNIOR, 1989 apud LEAL et al., 2005).
Calcule a capacidade para vários produtos - dificilmente as empresas produzem itens com o mesmo tempo padrão, sendo que a condição normal é que exista um mix de produtos disputando os mesmos recursos. Desta forma, deve-se apurar o tempo médio de produção (lembre-se que isto também vale para serviços) para cada produto no mesmo sistema de transformação e depois disso, calcular diversas combinações de capacidade, conforme a mudança no mix.
Obtenha a capacidade efetiva - neste passo são incorporadas as perdas planejadas, sendo que o conhecimento da base histórica para a mesma categoria de perda é um bom ponto de partida.
Monitore a capacidade realizada - a capacidade realizada trará o último estágio da análise e dependerá de uma boa forma de apontamento da produção e das paradas e seus motivos, para que não existem distorções. Em termos de planejamento e programação da produção o indicador de Quantidade Programada x Produzida por linha de programação trás sempre uma visão crítica em relação à capacidade realizada de uma planta fabril, devendo direcionar ações de melhoria em eventos kaizen.
Índices de Capacidade de Produção
Para finalizar este artigo trazemos três índices de análise da capacidade, que são úteis em momentos diferentes do processo de planejamento e de gestão da capacidade. Com intuito de aumentar a precisão para a tomada de decisão abordaremos os índices de eficiência, utilização e disponibilidade.
A capacidade instalada e a capacidade disponível permitem a formação de um índice, denominado grau de disponibilidade, que indica, em percentual, quanto uma unidade produtiva está disponível, conforme a fórmula abaixo (1):

A utilização representa sua produção efetiva dividida por sua capacidade disponível, ou de projeto, conforme representado na fórmula (2):
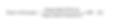
A capacidade realizada, que pode ser também convertida em horas trabalhadas, quando comparada à capacidade efetiva, que está relacionada às horas disponíveis; fornece o percentual de eficiência da unidade produtora em realizar o trabalho programado, conforme a fórmula (3), abaixo:

Adicionalmente, ao ter o conhecimento da eficiência produtiva da sua empresa (após saber se ela está operando com a capacidade de produção máxima), fica mais fácil inclusive analisar que ações e investimentos que precisam ser feitos para aumentar a produção. Baixos índices de eficiência, por exemplo, podem revelar para a oportunidade de melhorar o controle da qualidade das matérias-primas ou para melhor gestão da manutenção ao invés de investir em mais maquinário ou na abertura de novos turnos de produção. Lopes et al. (2003) conceituam paradas técnicas e organizacionais, sendo as primeiras relacionadas a paradas não planejadas e as últimas a planejadas. Os autores afirmam que "os tempos organizacionais devem ser considerados no cálculo da capacidade da célula, pois estão inclusos no tempo de operação". Por este motivo, os fatores que influenciam a capacidade necessária de um centro de trabalho são a eficiência, os refugos e os retrabalhos realizados durante o processo produtivo .
Considerações finais
Atendimento à demanda, custos e lucratividade são temas caros a qualquer empresa privada e objetivos finais da maioria dos gestores. O planejamento e a gestão da capacidade do sistema de transformação são essenciais para que esses objetivos sejam atingidos, uma vez que trás o conhecimento sobre a capacidade de geração de outputs para uma quantidade de recursos de transformação existentes.
Caso você queira ajuda para a maximização do uso de sua capacidade de sua estrutura de operações, a EXCENT Consultoria pode tornar esta jornada mais fácil e rápida.
Bibliografia
LEAL, F. et al. Uma ferramenta de ensino para análise de tempos nas relações de trabalho. In: SIMPÓSIO DE ENGENHARIA DE PRODUÇÃO - SIMPEP, 12., 2005, Bauru, SP, Brasil. Anais.
LOPES, M. T. R. et al. Uma abordagem para o estudo de tempos considerando paradas técnicas e organizacionais: um estudo de caso. In: ENCONTRO NACIONAL DE ENGENHARIA DE PRODUÇÃO - ENEGEP, 23., 2003, Ouro Preto, MG, Brasil. Anais. 2003.
SLACK, N.; CHAMBERS, S.; JOHNSTON, R. Administração da produção. 2. ed. São Paulo: Atlas, 2002.
WATTS, T. et al. Structural limits of capacity and implications for visibility. Journal of Accounting &Organizational Change, v. 5, n. 2, p. 294-312, 2009. http://dx.doi.org/10.1108/18325910910963472