- 12-02-2020
- Articles
Zamak: an allow with its own History and values
The history of Gurelan begins with Zamak, an outstanding material that emerged from the union between experience, technology and need. At the beginning of the 20th century, a growing world steel industry claimed for cheaper, more resistant and easy-to-mould materials. Now we tell you about it.
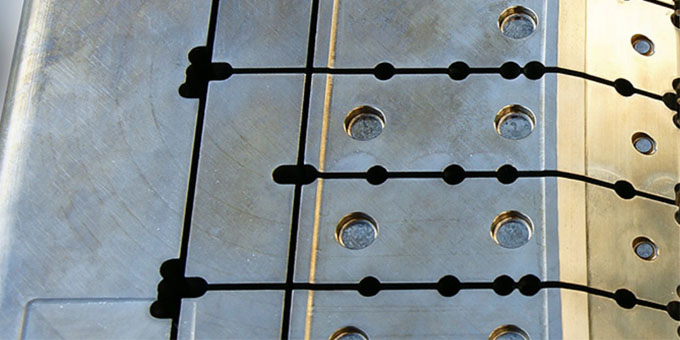
First of all, it´s good to refresh History a bit. The alloy called Zamak appeared between 1926 and 1929, when it was developed and patented by the New Jersey Zinc Company, a company that led the greatest research and achievements in the world of zinc at the beginning of the 20th century.
At that time, the steel industry demand for materials with special properties was constantly growing, as well as the resulting applications and by-products. Foundries needed a cheap, hard and resistant material easy to mould and mechanise. The aim was to obtain partswith higher precision, better finishing and higher quality than silver, which gets dirty and cannot be painted.
Initially named ´Zama´ or ´Mazak´, the New Jersey Zinc Company eventually decided on the term Zamak, to emphasize the importance of zinc as its main component. This word is composed of the German initials for the elements constituting the alloy: Z (Zinc), A (Aluminium), MA (Magnesium) and K (Kupfer, copper).
Zamak hot-chamber die casting, how does it work?
The manufacture of Zamak products involves a dedicated industrial process, determined by the final application of the part. For example, Gurelan manufactures Zamak parts for the automotive industry, locksmithery, jewellery, electronics... But how do we go from the raw Zamak ingot to a machined and finished safety part for vehicles?
To begin with, hot-chamber casting can be used with alloys melting at low temperature such as zinc, magnesium... It can be done either in in-house moulds - such as those made exclusively by Gurelan - or in standard moulds. Hot-chamber casting is suitable for metals that do not easily attack or erode equipment such as metal vats, cylinders and plungers.
Do you know that Zamak is an easy-to-mould material ?
Zamak ingots are melted in an oven at approximately 420 ºC located next to the moulding machines. The melted Zamak is then injected into the machinery chambers with high precision, in order to obtain parts of different sizes, weights and purposes.
The use of Zamak, thanks to its fluidity and its low melting temperature, allows to obtain extremely precise parts with very complex shapes and profiles. As a family company founded in 1934 for the manufacture of cutlery (shearing machines, shavers...), Gurelan pioneered the incorporation of hot-chamber machines for parts made from zinc alloys (Zamak), intended for the manufacture of these tools.
Why Zamak injection and not other alloys ?
Three simple reasons: quality, precision and production. It is very complicated to manufacture this type of parts using other alloys than Zamak, while keeping control of the costs as well as the industrial characteristics of the product. In fact, to perform machining, turning, polishing and finishing operations on a Zamak part is more economical and simple than, for example, on a brass part..
Another great advantage: the moulds for Zamak die casting have an useful life that can reach millions of cycles in many cases . For example, in Gurelan we own moulds that have exceeded 4 million cycles in multi-cavity. On the other hand, an aluminum mould will have a more limited life, thus generating a higher cost that will affect the final price of each injected part.
Therefore, thanks to an easy industrialization, a fast cycle and a low melting temperature, the pressure die casting of Zamak parts creates the perfect meeting point between costs, precision, durability and constant quality, both in small and large productions.