Spritzguss Spritzgussteile richtig konstruieren
Anbieter zum Thema
Bei der Konstruktion von Kunststoffbauteilen, die im Spritzgussverfahren hergestellt werden, lauern einige Fehlerquellen. Folgende Konstruktionsregeln können teure und zeitaufwendige Werkzeugänderungen ersparen.
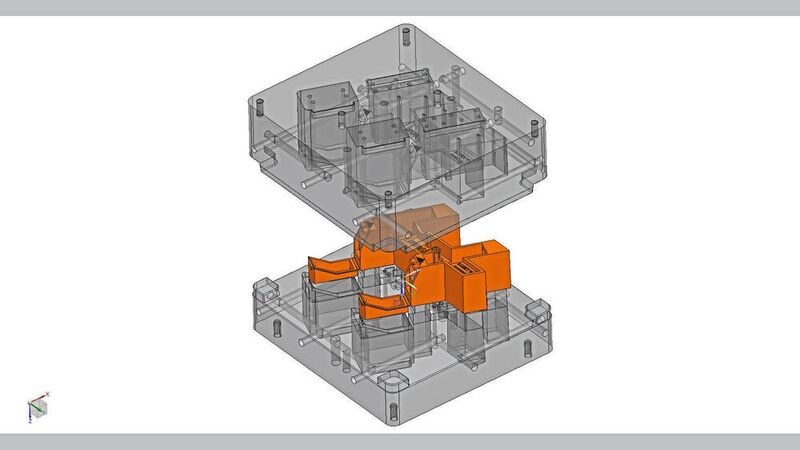
Ein Spritzgusswerkzeug besteht in der Regel aus zwei Formhälften. Diese ergeben sich durch die Hauptentformrichtung. Dabei definiert die Hauptentformrichtung, in welche Richtung sich das Werkzeug öffnet. Neben den Hauptentformrichtungen gibt es noch die sogenannten Nebenentformrichtungen. Diese entformen jene Bereiche, die in die Hauptrichtung nicht entformbar sind. Dies geschieht in der Regel durch Schieber oder Schrägauswerfer. Somit ist in der spritzgussgerechten Konstruktion der erste zu beachtende Faktor die Entformbarkeit des Artikels.
Entformschrägen festlegen
Sind die Entformrichtungen festgelegt, können die Entformschrägen an den Flächen angebracht werden. Im Spritzgussprozess kommt es beim Erstarren der Schmelze zu einem Aufschwinden auf die Werkzeugoberfläche – das Teil haftet im Werkzeug. Die Entformschrägen helfen dabei, das Bauteil leichter zu entformen und verhindern, dass das Teil in der Form hängenbleibt. Die Bauteilgeometrie hat Einfluss auf den Entformwinkel: Je höher die Formteilwände, desto größer sollte der Winkel sein. Zudem ist der Winkel der Entformschräge vom Werkstoff und von der gewählten Oberflächenstruktur abhängig. Je rauer die Oberfläche, desto größer muss die Entformschräge gewählt werden. Ist der Winkel zu gering gewählt, kann die zu Entformungsriefen an der Oberfläche führen. Die Auswahl an Oberflächen im Bereich Spritzguss ist groß und reicht von hochglanzpolierten Flächen bis hin zu den unterschiedlichsten Narbungen und Strukturen. So beeinflusst die Oberfläche am Ende die optische Bauteilqualität. Wird beispielsweise die richtige Oberflächenstruktur gewählt, ermöglicht dies in Bereichen mit Massenanhäufungen, Einfallsstellen bis zu einem gewissen Grat zu kaschieren.
Hinterschneidungen vermeiden
Sogenannte Hinterschneidungen sind Bereiche, die nicht in Hauptentformrichtung entformt werden können. Hierzu zählen beispielsweise Schnapphaken oder Bohrungen. Um Hinterschneidungen zu entformen werden die Nebenentformrichtungen benötigt. Geschieht dies über Schieber oder Schrägauswerfer, sollte, wenn möglich eine optimierte Artikelkonstruktion gewählt werden. Diese Umsetzung zählt zur kostenintensivsten Variante. Werden formschlüssige Kerne eingesetzt, können damit die Werkzeugkosten gesenkt werden. Hierbei stellt der Formkern durch eine Öffnung am Bauteil die Hinterschneidung her. Damit ist eine Entformung in Hauptentformrichtung möglich. Bei der Konstruktion von Schnapphaken und Rastnasen wird diese Technik sehr oft angewendet.
Das Kompetenzzentrum für Carbon- und Kunststofftechnik
Kunststoffelemente sind ein fester Bestandteil des alltäglichen Lebens. Doch erst durch das Spritzgießen können Gegenstände in die gewünschte Form gebracht werden. Eine extreme Prozessstabilität, geringe Teilekosten bei hohen Stückzahlen und die unmittelbare Verwendbarkeit der über Spritzguss erzeugten Formteile sind nur einige der Vorteile, die für das Verfahren sprechen. Beim österreichischen Familienunternehmen Hintsteiner Group im steirischen Kindberg treffen technologisches Know How und jahrzehntelange Entwicklungserfahrung auf ausgeprägte Pioniermentalität und Leidenschaft für unkonventionelle Lösungen.
Im Jahr 1981 mit dem Fokus Kunststofftechnik gegründet, entwickelt und fertigt die Hintsteiner Group heute auf 3500 m² in zwei Technologie-Sparten: Carbontechnik und Kunststofftechnik.
Die Zwangsentformung
Eine weitere Entformungsmethode ist die Zwangsentformung. Diese Methode funktioniert nur bei geringen Hinterschneidungen, denn Zwangsentformungen sind stark vom Material abhängig. Deshalb ist diese Methode nur bedingt zu empfehlen. Das Design der Hinterschneidung spielt eine wichtige Rolle. Wird das Kunststoffteil entformt, drückt sich die Formteilwand so weit weg, dass das Teil zwar leicht deformiert wird, aber nach der Entformung wieder nahezu in den Ursprungszustand zurückgekehrt.
Die richtige Wandstärke wählen
Die richtige Wandstärke zu wählen ist ein weiterer großer Faktor im Spritzgussprozess. Ist die Wandstärke etwa falsch dimensioniert, beeinflusst dies die Materialeigenschaften. Es gibt bestimmte Materialien, bei denen eine gewisse Mindestwandstärke nicht unterschritten werden sollte. Ist die Wandstärke beispielsweise zu groß, kann es zu Lunkerbildungen und Einfallstellen kommen. Einfallstellen sind Vertiefungen an der Formteiloberfläche, die teilweise nur am Glanzunterschied zur Umgebung erkennbar sind. Meist treten solche Einfallstellen im Bereich von Masseanhäufungen auf. Durch diese Masseanhäufungen entsteht eine lokal erhöhte Volumenschwindung, die die Oberflächenschicht nach innen zieht. Gibt die Oberfläche nicht nach, entstehen Lunker. Zudem erhöht eine zu groß dimensionierte Wandstärke die Zykluszeit und die Produktionskosten. Die Lösung: die betroffenen Bereiche auskernen. Dabei sollte auf eine gleichmäßige Wandstärke sowie die Entformungsrichtungen geachtet werden, damit keine ungewollten Hinterschneidungen entstehen. Ist die Wandstärke allerdings zu gering, kann es zu Problemen bei der Verarbeitung kommen. Dabei werden bei der Bauteilfüllung Bereiche nicht richtig ausgespritzt. Die Wandstärke sollte daher zwischen 1,5 mm und 4 mm liegen.
Versteifungsrippen richtig dimensionieren
Um die Bauteilsteifigkeit zu erhöhen, werden in der Regel Versteifungsrippen eingebracht. Je nach Belastungsart gibt es verschiedene Varianten von Verrippungen. Je mehr Rippen, desto steifer wird ein Bauteil. Jedoch bedeutet auch jede Rippe eine Materialanhäufung. Werden die Rippen und Kreuzungspunkte allerdings im Vorfeld richtig dimensioniert, kann eine solche Anhäufung vermieden werden. Sind die Verrippungen falsch dimensioniert, scheinen die Rippen an der gegenüberliegenden Oberfläche durch. Daher sollte immer auf das Verhältnis von Grundwandstärke zu Rippenstärke geachtet werden. Für eine optimale Dimensionierung liegt dieses Verhältnis bei 3:1.
Bei der Konstruktion von Verrippungen stellt sich auch die Frage der Verrundungen am Rippenfuß. Ein Radius bei Verrippungen und Ecken kann bei scharfkantigen Übergängen wie eine Sollbruchstelle wirken. Diese Radien sollten eher kleiner dimensioniert werden, max. 0,5 x Rippenwandstärke, da ansonsten wieder eine Materialanhäufung entsteht. Auch bei den Kreuzungspunkten der Rippen sowie bei der Anbindung an den Bauteilrand, sollten die Rippenmuster so konstruiert sein, dass es zu keiner Materialanhäufung kommt.
Zudem verbessern Rippen den Bauteilverzug. Beim Verzug weicht das Formteil von der gewünschten Form ab und zeigt Verschwindungen, Verwerfungen wellige Flächen oder Winkelabweichungen. Doch wie kommt es dazu? Die Ursache ist ein unterschiedliches Schwindungsbestreben verschiedener Formteilbereiche. Die Schwindungsdifferenzen entstehen durch unterschiedliche Verdichtung der Formteilbereiche und Orientierungen.
Simulation unterstützt beim Design
Die Simulation von Spritzgussteilen unterstützt beim Design. Hier können Konstrukteure beispielsweise die Bauteilfüllung und den Verzug simulieren. Die Ergebnisse fließen dann wiederrum in die Konstruktion ein. Simulationen von Spritzgussteilen und Werkzeugen lohnen sich aufgrund ihrer hohen Kosten bei hochkomplexen Bauteilgeometrien.
Die spritzgussgerechte Bauteilkonstruktion hängt von unterschiedlichsten Faktoren ab und muss individuell an das Bauteil angepasst werden. Ziel hierbei ist es, die Werkzeugkosten gering zu halten und aufwendige Änderungsschleifen im Idealfall zu vermeiden. Gleichzeitig soll eine hohe Bauteilqualität erreicht werden. Der Kompromiss zwischen Qualität und Kosten stellt Konstrukteure im Verlauf ihres Projektes vor große Herausforderungen. Hier können Experten im Bereich Konstruktion und Herstellung von Spritzgussteilen mit ihren Erfahrungswerten weiterhelfen. (jup)
(ID:48591594)