Metal Exterior Walls
A durable, sustainable, and aesthetic design solution for many building types
Continuing Education
Use the following learning objectives to focus your study while reading this month’s Continuing Education article.
Learning Objectives - After reading this article, you will be able to:
- Identify and recognize the characteristics of different commonly available metal wall panels and systems.
- Investigate the design potential and innovative opportunities to create buildings with attractive and durable exterior wall systems, canopies, and soffits.
- Assess the functional contributions of exterior metal walls as they contribute to green and sustainable design
- Specify metal exterior walls in a variety of green and conventional buildings and formulate appropriate selections related to specific applications.
The weathering skin of a building is also the visual skin that gives a building its character and aesthetic appearance. There are of course many choices of skin materials that architects can choose from with varying degrees of suitability for different building projects. In many cases, where economy, longevity, and lightweight materials are part of the preferred criteria, metal wall panels are the favored selection. In addition to meeting these basic design criteria, they have been proven over time in many different settings to be a reliable and sustainable design option.
Overview of Metal Wall Panels
Metal wall panels are manufactured by a variety of companies in the U.S. The industry trade group, known as the Metal Construction Association (MCA), views itself as a progressive organization that is supported by nearly 100 member companies, including metal panel manufacturers, coil coaters, distributors, fabricators, accessory and insulation producers, and contractors. Together, they advance industry-wide standards in metal panel fabrication and construction techniques as well as promote sustainable products and practices by its members.
The MCA has pointed out that recent improvements in the metal panel manufacturing process have resulted in a wider selection of metal panel products. This includes more choices in panel profiles and sizes allowing more choice and flexibility when considering metal panels in the design of a building. At the same time, new developments in coating technology allow longer life spans for the finished coating as well as the metal panels. As a result, the emergence of new product choices has allowed preformed metal wall panels to become a familiar part of mainstream commercial building design, and even some progressive residential buildings. All of this has contributed to a market trend where metal wall panels are currently used in greater quantities than metal roofing panels.
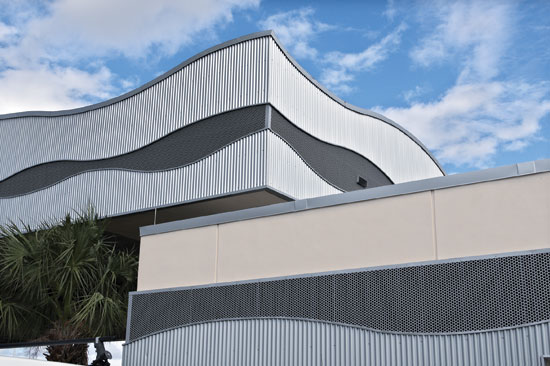
Photo courtesy of Petersen Aluminum / PAC-CLAD
Metal wall panels are an increasingly popular choice for exterior wall skins due to their versatility and range of profiles, colors, and design possibilities.
Preformed metal wall panels are available in either insulated or uninsulated versions. Insulated metal panel systems are generally comprised of an exterior weathering panel and an interior liner panel that is filled between with rigid insulation. Since it is more common to use uninsulated metal panels over an insulated wall assembly, this article will focus on preformed metal panels that are used in this way.
Preformed metal wall panels are manufactured from a variety of metals, including steel, aluminum, copper, and zinc. Copper and zinc panels are generally unfinished allowing them to develop a natural patina which is both a protective layer and an aesthetic contributor. Steel panels typically come with a highly durable paint or coating that is applied to the metal panels to protect them from the elements. Aluminum panels can be anodized or covered with a similarly durable paint coating such as Kynar or similar. The choice of colors ranges from standard hues to custom-matched tones to match a variety of design intents. Either way, when finishes are used, they are applied during the manufacturing process in a controlled environment to assure uniformity and control the quality and thickness of the finish.
Part of the popularity of preformed metal wall panels is attributable to their economic benefits. They have been compared to other wall / skin systems and are typically lower in installed cost than that of tilt-up wall systems, precast concrete or brick while coming out comparable to synthetic stucco or EIFS. Since they are a comparatively lightweight material, they have less impact on dead load allowing for reduced structural system sizing and cost than heavier wall materials. A more common reason given for their cost effectiveness is that metal wall panels can often be installed faster than other wall materials, resulting in corresponding labor and schedule savings. Since their installation is not slowed by weather conditions, they can minimize construction delays, allow for fast-track scheduling, and get the building enclosed or weather-tight quicker thus allowing other trades to proceed with interior work. Further, the myriad of metal panel design options available on the market offers the opportunity to add distinctive architectural effects to a building without necessarily altering the cost significantly.
Beyond first costs, the long-term cost of ownership is also very favorable. Their typical service life is 20 to 30 years, and can be even longer depending on the geographic location of the building and the surrounding environmental conditions. This longevity is attributable not only to the inherent durability of metal, but also to the highly durable metal coatings routinely used to protect them. These factory-applied coatings directly contribute to the low maintenance requirements of a metal wall system by preventing any corrosion that would otherwise require panel replacements. Further, since many of the coatings are exceptionally smooth, dirt doesn't stick while rainwater flushes them clean, meaning they require little or no maintenance.
Preformed metal wall panels are currently available in a wide choice of sizes, textures, colors, and profiles. It is usually the profile that makes the biggest difference on a building in terms of its textural appearance. Some of the more popular profiles include three that are discussed further here, specifically corrugated panels, flush and reveal panels, and composite panels, all of which can be used to create distinctive reveals, shadow lines and other architectural effects.
Metal Wall Panels
One reason for the growth of traditional corrugated metal wall panels, especially in the commercial market, is an inherent versatility offered by manufacturers. Traditionally, preformed panels of all sorts, but corrugated in particular, were only installed vertically. It has become more popular to use them horizontally and manufacturers have responded with fabrication and installation systems to accommodate that design need. This offers great design flexibility by combining bold visual effects with easy, cost-effective installation. Further, the corrugations, whether square, rounded, or trapezoidal, all create inherent strength and rigidity in the panel. Profiles are available that use either a concealed extended screw leg or a clip leg to link and clip panels together. In either case, the repeating rib and interlocking profiles provide a continuous integrated appearance that is cost effective in all weather conditions. Profiles are commonly available in panels of 12" or 16" widths with a common 7/8" panel depth and lengths up to 35 feet.
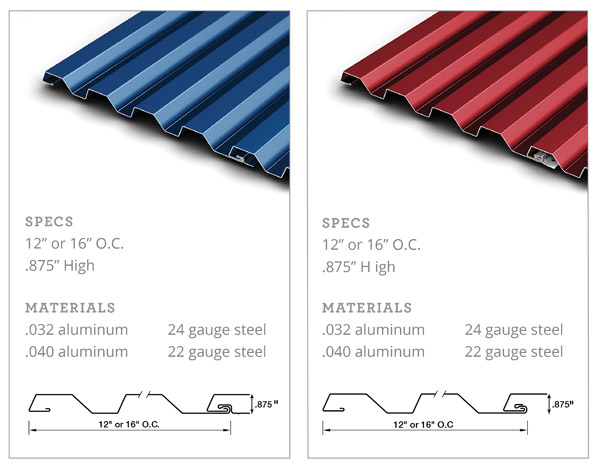
Images courtesy of Petersen Aluminum / PAC-CLAD
Corrugated metal wall panels have been used for decades in both vertical and horizontal design applications in different configurations.
Flush Panels
For design situations that seek flat or flush appearances, metal panels are available to meet this need, not only for walls but in matching products for fascia and soffit applications as well. Typically these panels use an interlocking leg on one side and concealed fasteners on the other to maintain a visually clean and flush appearance while providing additional strength. The panels can be factory-formed to length to minimize field cutting with common maximum panel lengths of 25 feet and minimum lengths of 4 feet.
In selecting flush panels, there are two different aesthetic options – selecting panels that butt tight to each other with only the joint showing or panels that create an intentional reveal space between them. Both of these profiles allow for strong design statements and are available in a full range of colors. Both are intended for use in vertical wall, fascia and soffit applications but are not appropriate profiles for roofing or mansard applications. (Metal roofing products are available for those applications.) In cases where longer panel lengths are desired, stiffening boards behind the panels are recommended to maintain and protect the shape of the panel.
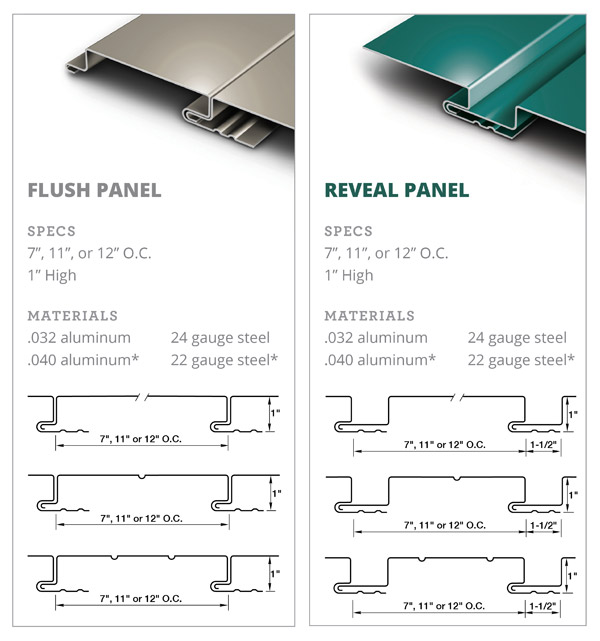
Images courtesy of Petersen Aluminum / PAC-CLAD
Flush wall panels are flat across their face and are commonly available in panels that create a very tight joint (shown on left) or an intentional reveal (shown on right).
Flush panels are formed by some manufacturers on precision roll-forming equipment that uses a system of corrective levelers. Corrective leveling works to remove typical metal conditions including coil set, crowning and edge wave. In-line leveling capabilities allow the metal material to be "still-water" flat so the finished panel is truly flush. The result is a panel that can exhibit superior flatness without any extra cost.
Flush Panels should be installed over the exterior sheathing or other substrate in an exterior wall assembly with an appropriate air and water vapor barrier in place. Flush panels can be used in a rainscreen application as long as water is allowed to drain out from behind the panels. When used in a windscreen application, panels must be fastened (stitched) through side joints. There is also the option of using exposed fastener systems with flush panels where the conditions and aesthetics warrant it.
Exposed Fastener Panels
Exposed Fastener Panels provide the most flexibility for use in wall, interior and linear panel applications. They are a cost-efficient yet architecturally appropriate metal panel solution in many cases. Available in several coverage widths, exposed fastener panel profiles are available in a full range of gauges and materials. Exposed fastener panels can also be produced in a perforated pattern for a variety of exterior projects, such as equipment screens or for interior acoustical applications. Manufacturer's technical staff can be a resource to review exposed fastener panel options including panel material selection, finish specification, and budgeting.
Composite Wall Panels
Metal Composite Material (MCM) panels combine some of the strong aesthetics of flush panels with the rigidity of corrugated panels. Typically, MCM panels create a smooth, sleek look that can be bent, curved and joined together in an almost limitless range of geometric configurations. Originally called aluminum composite materials (ACM), the name of the product category changed to metal composite materials to reflect the introduction of other skin metals, such as zinc, copper, stainless steel, and titanium. Aluminum, however, remains the predominant skin material in use.
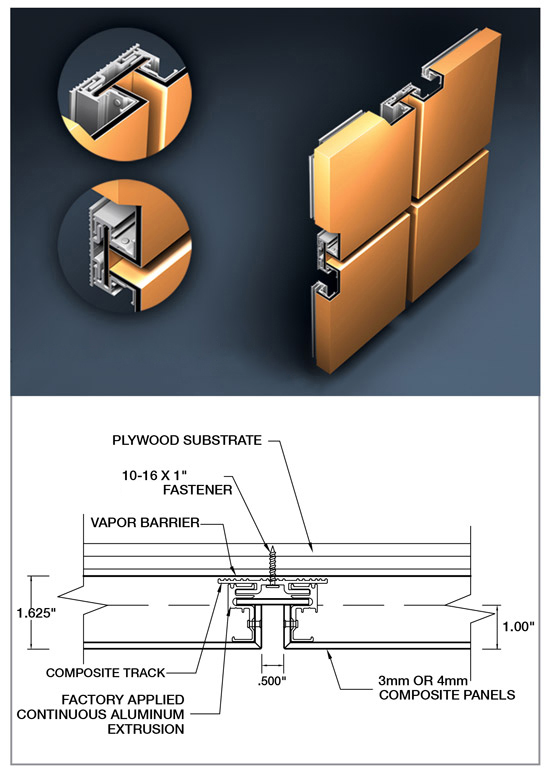
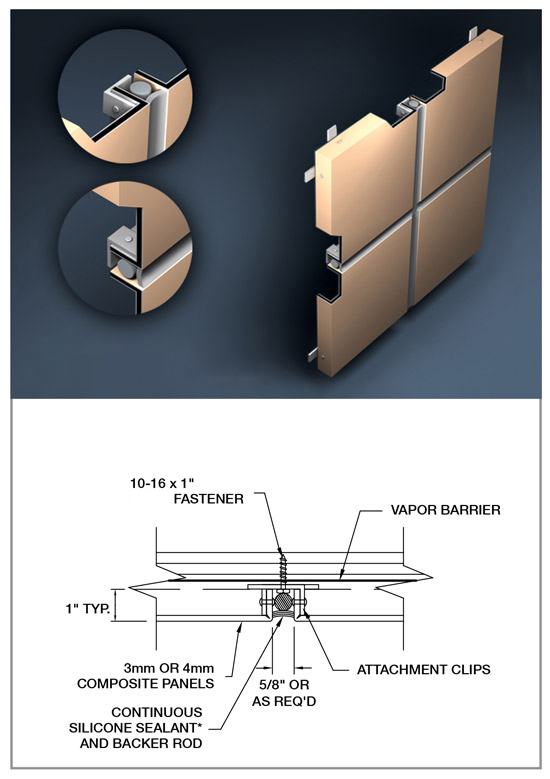
Images courtesy of Petersen Aluminum / PAC-CLAD
Composite metal wall panels are flat and lightweight using two layers of metal with an engineered plastic layer in between.
The Metal Construction Association notes that MCM panels have been used in North American construction projects for nearly 30 years and the market trends show their use to be increasing more and more. They are formed by bonding two metal skins to a highly engineered plastic core (polyethylene or fire-retardant plastic) placed between them, creating a thin "sandwich" panel. The bonding process necessarily occurs under very precise conditions of temperature, pressure and tension. Some panels are formed by a rout and return process utilizing computer controlled routing equipment. This state-of-art fabrication insures tight tolerances and accurate panel dimensions. The result is a metal/plastic composite sheet that provides numerous benefits compared to a similar thickness of a solid metal sheet. For example, MCM sheets are flat when manufactured and have been proven to stay flat after installation. There is no "oil canning" or wrinkling because the skins are bonded to the core. MCMs also provide a wide variety of finish since aluminum and steel MCMs are available in virtually any color a building owner or architect wishes. Current paint application technology helps to ensure that the finish remains consistent between panels eliminating the possibility of a checkerboard appearance of mismatched panels on the building's exterior.
While strong aesthetics is one reason for the popularity of MCMs affordability is another. When first introduced, MCMs were limited to use on high end projects but improvements in manufacturing technology, efficiencies in installation and good old fashioned competition have made these panels very cost-competitive. Construction costs are often lower with MCM panels because they can be installed faster than alternative exterior skins and their light weight reduces structural requirements. All of this means that MCM panels are found on a wide variety of building types and metal building applications, ranging from wall panel systems on major projects to cornices and canopies on smaller ones.
Properly designed and installed, MCM panels provide a very reliable and versatile building skin. MCM manufacturers commonly produce the high quality metal sheets in a wide variety of lengths and widths. It is the metal fabricators however who change the flat sheets into panels that are custom sized and suited for use in particular buildings. In some cases, the fabricators may also install the system. Typically staggered angle clips mounted to the panels allow for each panel to be installed and adjusted individually in the field for a proper fit.
Design Applications
Historically, preformed or roll-formed metal wall panels were used almost exclusively on industrial plants and warehouses since they were viewed as a durable, reliable and affordable building skin option. However, they have been increasingly seen as a strong design element in recent times such that they are used on virtually every type of structure, from manufacturing facilities and stores to schools and office buildings.
New Buildings
The variety of appearances and profiles available for metal wall panels has made them a very popular choice for a number of new building types. Retail buildings benefit from the striking colors that can be customized and used in multiple store locations. K-12 schools that need durable and affordable materials benefit from a high quality, long lasting exterior skin that can be customized for a variety of communities and learning intentions. Commercial buildings such as offices, hospitality buildings, churches and others all find options and styles to suit differing needs. Higher education buildings that seek to make bold statements with their siding and convey a forward thinking design approach can use metal panels mixed with other materials to achieve this intent. Similarly, health care buildings that strive for a soothing combination of materials can achieve that look with preformed metal panels.
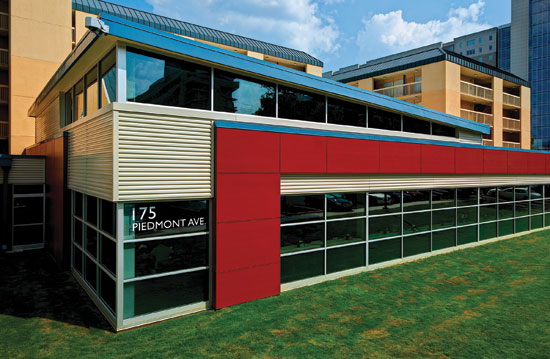
Horizontal metal wall panels in a metallic color are integrated with the rest of a building facade at Georgia State University.
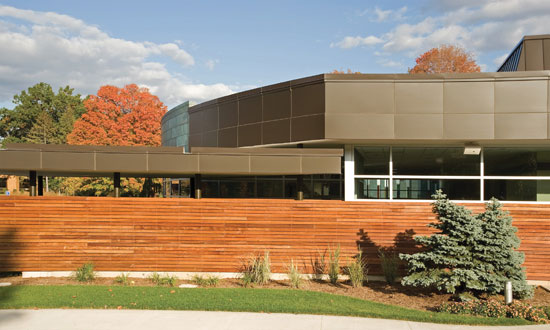
Photos courtesy of Petersen Aluminum / PAC-CLAD
Composite panels blend with other natural materials and the surrounding area at the Pine Rest Postma Center.
Existing Buildings
A large and growing part of the use of metal wall panels is the renovation and rehabilitation of existing buildings. Building exteriors that are either worn or deteriorated or are in need of a new look due to use or ownership changes find an efficient and effective option in metal panels. In particular, recovering or resurfacing canopies, soffits, and fascia are common in many building types but schools and retail stores in particular. The use of these metal wall panels creates a new look and can completely rejuvenate a building while respecting construction budgets. In many cases, some of the existing façade material may be able to remain in place minimizing work and waste as long as the new panels can be securely and properly installed. While, in some cases metal panels are used to add insulation to an exterior wall, it is more common to see uninsulated panels in a selected type and profile being used as a new skin for improved appearance and weathering. In the case of special or unique façades that require custom installations, the flexibility of metal panel sizing and fabrication means that custom work can be readily accomplished and installed using traditional methods.
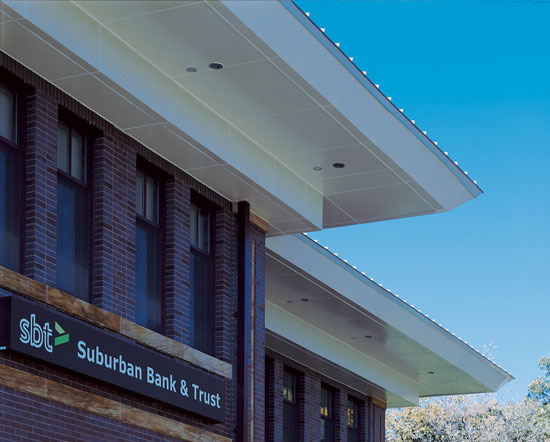
Photo courtesy of Petersen Aluminum / PAC-CLAD
Retrofit metal soffits and fascia using flush composite panels give an existing bank building a fresh new look and improve the weather-ability of the structure.
Green Building Contributions from Metal Exterior Walls
The MCA points out that metal wall panels are an environmentally responsible and sustainable design choice that features high recycled content, low maintenance and long service life. In addition, the metal used in the panels is 100% recyclable at the end of its useful life.
The US Green Building Council (USGBC) has developed the LEED® rating system for green buildings which has been recognized as the leading green building standard in this country. The LEED 2009 system is in place until the year 2015 which overlaps with LEED version 4 introduced late in 2013. Since buildings are currently being designed under both systems, credits available for both are summarized below through the use of preformed metal wall panels.
Sustainable Sites
Under LEED 2009, credit 7.2 is available for reducing the heat island effect. This is primarily for roofing systems and makes 1 point available. Since many metal wall panel manufacturers also produce metal roofing panels they have developed products that meet the criteria to reflect heat and thus reduce the heat island effect. Under an innovation credit, it may be possible to show that the same heat reflective qualities are available in wall panels and therefore help reduce environmental heat build-up.
Optimize Energy Performance
Both LEED 2009 and LEED v. 4 place a strong emphasis on reducing the use of fossil fuels and increasing the use of non-polluting renewable energy. Cool metal wall and roof products have been shown to contribute to excellent thermal performance by reflecting away unwanted heat from the building as well as the surrounding site. In order to receive points in this credit category the building must demonstrate a percentage increase in energy savings in accordance with ASHRAE standards. The number of points available depends on the degree of energy savings.
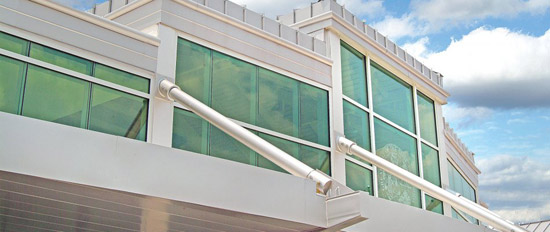
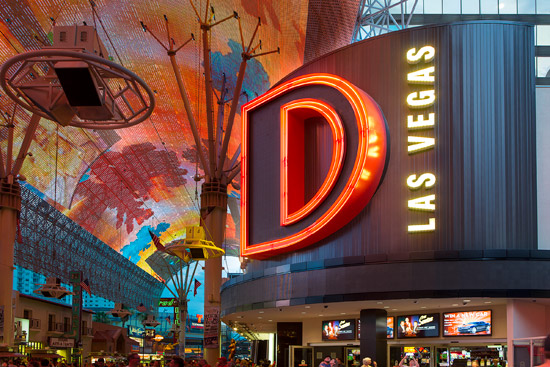
Photos courtesy of Petersen Aluminum / PAC-CLAD
Flush panels used for siding and soffits at the Florida Welcome Center help reflect heat and add to the energy efficiency of the building while creating a vibrant look at the D Casino in Las Vegas.
Materials and Resources
This area has changed dramatically between the different versions of the LEED® rating system. LEED 2009 includes four areas where metal wall panels can contribute to an overall green building:
• Credit 1.1: Building Reuse: Maintain 55%, 75% or 95% of Existing Walls, Floors and Roof (1-3 points) Metal panels can be salvaged and re-used in existing buildings that are being renovated.
• Credit 2: Construction Waste Management (1 -2 points) The single component nature of custom fabricated metal wall panels limits scrap material and reduces construction site waste accordingly. Further, any excess material is fully recyclable so that it is fully diverted from the waste stream and disposal.
• Credit 3: Materials Reuse: 5% or 10% (1 or 2 points) Metal wall panels that can be salvaged or re-used from an existing building can contribute directly to this point.
• Credit 4: Recycled Content: 10% and 20% (1 – 2 points) In theory, there are no limits on the recycled content of metal building panels – it can go all the way to 100%. As a practical matter, the following are more common recycled content levels:
• Aluminum – up to 85 percent total made up of approximately 60 percent post-consumer and 25% pre-Consumer
• Steel – between 28 – 35 percent total made up of approximately 25 percent post- consumer and approximately 7-1/2 percent pre-consumer
• Credit 5: Regional Materials (1 – 2 points). Many metal wall panels are manufactured in the USA meaning a regional material contribution is possible depending on proximity to the building.
The Materials and Resources category under LEED v. 4 takes a rather different approach to defining the green nature of building products. There are still credits for Building Re-use and Construction Waste Management, but the rest of the approach focuses on the full life cycle of those products. The key documentation needed to demonstrate performance under this approach is referred to as an Environmental Product Declaration (EPD). Individual manufacturers or a trade association can prepare specific or generic EPDs for products. In the case of metal wall panels, the MCA has prepared and released such a document that covers the range of metal wall panels on the market. The overall intent is to address an emphasis on transparency in the sourcing, ingredient, and manufacturing processes as called for in LEED v. 4.
EPDs are intended to provide Life Cycle Analysis based information and details about the products' environmental aspects thus assisting purchasers and designers in making informed comparisons between products. The MCA industry-wide EPD contains valuable facts about product definition, building physics, the basic material and its origin, product manufacture and processing, in-use conditions, life cycle assessment results, and testing results and verifications. Environmental impacts are assessed throughout the product's lifecycle, including raw material extraction, transportation, manufacturing packaging, use, and disposal at the end of a building's useful life. All content in the document has been reviewed by a UL Environment Review Panel and independently verified in accordance with ISO 14025 and ISO 14044.
Specifying Metal Wall Panels
When specifying metal wall panels, there are choices and specification details to pay attention to so that the best products are selected for the building where they will be installed. The Master Format section number commonly used is 07 41 00 for metal roof and wall panels. Some of the relevant items to address in a standard 3-part specification format are highlighted as follows.
Part 1 - General
Quality assurance is often addressed by citing specific national testing and standards for products. In the case of metal wall panels, there are a full range of appropriate tests that have been developed and are accepted by the industry including the following for the basic sheet metal used:
• ASTM A653 Standard Specification for Steel Sheet, Zinc-Coated (Galvanized) or Zinc- Iron Alloy-Coated (Galvannealed) by the Hot-Dip Process
• ASTM A792/A792M Standard Specification for Steel Sheet, 55 % Aluminum-Zinc Alloy- Coated by the Hot-Dip Process
• ASTM B209 Standard Specification for Aluminum and Aluminum-Alloy Sheet and Plate
There are also standards for the performance of wall assemblies that will apply to those that use metal wall panels:
- ASTM E283 Standard Test Method for Determining Rate of Air Leakage Through Exterior Windows, Curtain Walls, and Doors Under Specified Pressure Differences Across the Specimen
- ASTM E331 Standard Test Method for Water Penetration of Exterior Windows, Skylights, Doors, and Curtain Walls by Uniform Static Air Pressure Difference
- ASTM E1592 Standard Test Method for Structural Performance of Sheet Metal Roof and Siding Systems by Uniform Static Air Pressure Difference
When it comes to fire testing of exterior systems, the following may be applicable depending on the wall design:
- UL 263 Fire Tests of Building Construction and Materials
- ASTM E-84 standard for fire testing of materials
Other General specification information includes the appropriate request for submittals that confirm the correct metal wall panels are being ordered and fabricated. Obviously some of this is useful during design while under an integrated project delivery process, the fabricator may be brought in during the design stage. In any case, a full warranty should be called for and submitted that demonstrates coverage for up to 20 years including cracking, peeling and color fade at a minimum.
Part 2 - Products
Identifying the specific metal wall panel products that are desired requires covering several items. If multiple product types are selected for a building, then obviously they each need to be specified and their locations identified on the drawings.
- Panel type and profile: the particular type of panel needs to be selected such as corrugated, flush, or composite (MCM). Within the type(s) selected, then a specific profile needs to be identified to be sure that the desired appearance is achieved.
- Metals: Fundamental to the panel is the choice of metal being used. The choice may be influenced on the difference in environmental impact between say aluminum and steel and the degree to which they contain recycled material. Zinc or copper alloy may also be preferred based on the ability to avoid an additional finish and a potentially much longer service life as a result.
- Attachments: Concealed fastening is most often preferred for aesthetic reasons and will thus dictate specific attachment methods consistent with the panel design and profile. Keep in mind that dissimilar metals should not be used to avoid galvanic corrosion from the interaction of those metals. In cases where exposed fasteners are acceptable, then those should be specified accordingly, usually with self-sealing washers of neoprene or similar materials. In coastal conditions, it is advisable to use stainless steel fasteners with painted steel panels.
- Trim: Flashing and trim may be needed to make the wall panel system complete and weather tight. In that case, it should be fabricated by the manufacturer or a qualified fabricator out of matching material. Aluminum trim may be .032 – .063 gauge or steel can be 24 gauge or 22 gauge as appropriate.
- Finishes: Since all metal wall panels come pre-finished from the manufacturer finish selections need to be clearly and precisely made. The full range available from a particular manufacturer should be identified depending on the type of metal used and whether they are anodized, natural, or painted finishes.
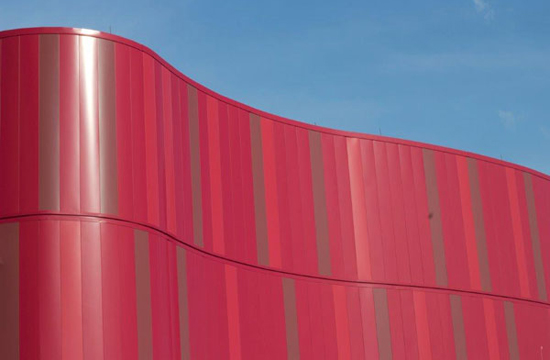
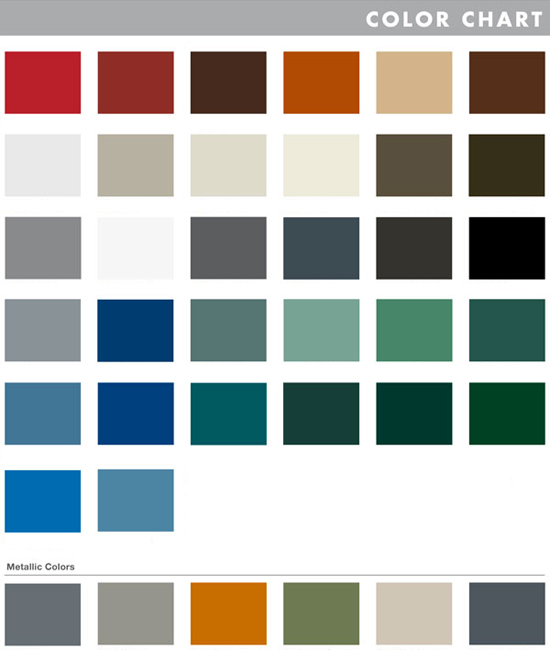
Images courtesy of Petersen Aluminum / PAC-CLAD
A sample of the range of colors available from one manufacturer of prefinished and preformed metal wall panels.
Since some aspects of products vary between manufacturers, using the specification items above will aid in product to product comparisons during design and assure appropriate installations during construction.
Part 3 - Execution
Installing metal wall panels is fairly straight forward but requires appropriate attention to detail to assure the desired outcome is achieved.
- Examination and Preparation: The rest of the exterior wall assembly needs to be in place with the requisite air and water barrier already installed. This should all be inspected for completeness and conformance with the building design before the metal wall panels are installed.
- Installation and Field Quality Control: Since it may be the fabricator that is doing the installation, the qualifications of that fabricator should be known ahead of time. In many cases, the manufacturers have specific instructions or recommendations on how to best install the products they produce so these should be referenced and followed.
- Vinyl masking: In cases where a lot of handling is anticipated, vinyl masking is usually recommended and installed on all fabrications. Manufacturers will suggest that this strippable vinyl film must be removed immediately after installation to avoid marking or undue difficulty in removing it later.
- Cleaning and Protection: The nature of the panel finishes is to be very smooth and easy to clean. In most cases, dust and dirt from construction can be easily wiped clean with a soft cloth or rinsed with water. If needed, a common soap and water rinse can be used to clean the panels.
Conclusion
Preformed metal wall panels have a long history of successful applications in buildings of many types. They are currently available in a wider array of types, profiles, colors and options than ever before. They have been gaining in popularity in both new buildings and the renovation of existing buildings. Their initial and long term costs have been shown to be favorable in many applications. From a green building standpoint, they can contribute in a variety of ways due to their inherent ability for long term sustainability and recyclability. They can be readily specified from national manufacturers for local fabrication and installation to produce design and performance results that are attractive and favorable all the way around. Overall, these attributes and performance positions preformed metal wall panels as a very viable choice for exterior wall applications on commercial, institutional, and residential buildings of all types.
![]() |
Petersen Aluminum Corporation produces a complete line of architectural metal products: Metal Roofing & Wall Panels, Composite Wall Panels, Column Covers, Soffit, Coping, Flashing and Trim. Most of the 38 PAC-CLAD® Kynar 500® color finishes meet LEED® & ENERGY STAR® requirements. |