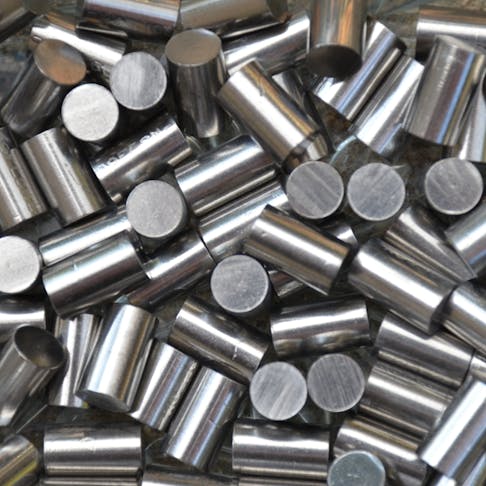
Alloys: Definition, Composition, Types, Properties, and Applications
Learn more about these metals and how they are used in manufacturing.
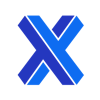
Alloys are metals comprising two or more metals or a base metal with non-metallic additions. The addition of various elements to a pure metal’s lattice structure enables metals to have properties that they do not display in their pure forms. In general, alloys are stronger, harder, more durable, and sometimes more corrosion-resistant than their pure metal counterparts. The exact composition of an alloy will vary depending on the type of base metal and its alloying elements. Examples of alloys include steel, brass, and aluminum alloys. Alloys are used in a wide range of applications, from construction and transportation to jewelry and art. This article will explain what an alloy is and review the different types, compositions, and applications.
What Is an Alloy?
An alloy is a material composed of a metallic base and additional metal or non-metal elements. Alloys are typically created to obtain desirable material properties that otherwise are not present in the primary base material’s pure form. While metals are commonly used as alloying additions, non-metals, primarily, are often used too.
What Is the History of Alloys?
Alloys have been used as early as 3000 BCE. The first known alloys were brass (a combination of copper and zinc) and bronze (a combination of copper and tin). They were primarily used to make tools and weapons. In the 16th century BCE, wrought iron and cast iron — two alloys made from iron and carbon — were created by hammering hot iron over a flame. The carbon from the flame diffused into the iron structure. These two alloys were the predecessors to carbon steel. However, it wasn’t until the Industrial Revolution in the 18th century that many of the alloys commonly used today were developed. Advances in chemistry allowed the isolation of metallic elements such as manganese, nickel, and chromium, which enabled the creation of stainless steel, aluminum, titanium, nickel, and many other alloys commonly used today.
What Is Another Term for Alloy?
A few other terms for “alloy” are: mixture, fusion, amalgam, solid solution, and admixture.
What Is an Alloy Made Of?
Alloys are metallic materials comprising a base metal and additions of other metals, non-metals, or both. The exact composition of an alloy can vary widely depending on the base metal, its alloying elements, desired properties, and intended application.
How Are Alloys Made?
Alloys are made by melting and mixing the base metal and additional elements (metals and/or non-metals) and allowing them to cool. Two types of alloys exist: substitutional alloys and interstitial alloys. In substitutional alloys, like brass and bronze, the atoms of the alloying elements are similar in size. The atoms of the alloying elements occupy, or substitute, the same sites the atoms of the base material would occupy in its lattice structure. In interstitial alloys, like steel, the atoms of the alloying elements are smaller and fit in between the atoms of the base metal. After mixing, the alloys can be cast or wrought into ingots, rods, bars, or plates.
What Are the Characteristics of Alloys?
While characteristics will vary widely depending on the type of alloy, the general characteristics of alloys are listed below:
- Improved Properties: Alloys are created by combining two or more metals or elements. The resulting material typically has improved properties compared to its constituent parts. For example, steel is stronger and more durable than iron alone, and bronze is harder and more corrosion-resistant than pure copper.
- Customizability: Alloys enable desirable properties that do not exist in the original pure metals to be obtained. For instance, aluminum alloys are much stronger and harder compared to pure aluminum, which is soft and malleable.
- Diversity: Several hundred different alloys currently exist. Alloys have been created to serve many different applications. New alloys are also constantly being developed.
- Strength: Alloys are stronger than their pure metal counterparts. Additional elements in the base metal’s lattice structure make it harder for atoms to move around, which makes the material stronger.
- Corrosion Resistance: Alloys are more corrosion-resistant than pure metals. Additional alloying elements interact with the air and form a protective oxide layer on the surface of the alloy.
- Electrical Conductivity: Alloys tend to have lower electrical conductivity than pure metals. The addition of atoms with different charges in the lattice structure of the base metal can interfere with the flow of electrons through an alloy.
- Thermal Conductivity: Alloys tend to have lower thermal conductivity than pure metals. A metal’s ability to conduct heat is dependent on the number of free electrons within its atoms. The addition of atoms with different charges in the lattice structure of the base metal can interfere with the flow of electrons through an alloy.
What Is the Color of an Alloy?
The colors of alloys vary based on their composition. Alloys will generally have a color similar to that of the base metal but may appear lighter or darker depending on the additional elements.
What Does an Alloy Look Like?
Alloys are similar in appearance to their base metals but may appear lighter or darker in tone depending on the alloy’s composition. Pure copper has an orange tone, while bronze appears reddish-brown and brass appears like dull gold. Both bronze and brass contain copper. Figure 1 below shows some examples of alloys:
Colors of common alloys.
Image Credit: https://studiousguy.com/
What Are the Different Types of Alloy?
The most common classes of alloys are listed and described below:
1. Steel
All steels are based on the element iron with a small amount (<2%) of carbon added. Other intentional alloying elements added to improve or alter the properties of steel include manganese, nickel, chromium, and vanadium. Many other elements may be added for specific purposes, and or be present as residuals. While exact properties may differ based on chemical composition, in general, when compared to pure iron, steel is stronger, harder, and tougher, but less ductile. Some steel alloys, such as stainless steel, are also corrosion-resistant. Steel is one of the most commonly used metals today. It is often used in buildings, ships and watercraft, automobiles, medical equipment, household appliances, and tools. For more information, see our guide on Steel Alloy.
2. Brass
Brass is an alloy composed of approximately 66.6% copper and 33.3% zinc. However, many brass alloys that are variations on this basic formula have been developed. These may contain such additional alloying elements as aluminum, antimony, iron, or silicon. In general, brass is stronger, harder, less dense, and more easily machinable than pure copper. Brass is often used in buttons, hardware, ammunition cartridge cases, and marine applications.
3. Bronze
Bronze is an alloy composed of approximately 88% copper and 12% tin. Additional elements such as aluminum, phosphorus, manganese, and silicon are also sometimes added. Compared to pure copper, bronze is stronger, harder, more corrosion-resistant, and easier to cast. Bronze is often used in sculptures, gears, bushings, and tools.
4. Aluminum Alloys
Aluminum alloys are made by combining aluminum with smaller amounts of elements such as manganese, copper, magnesium, silicon, and zinc. Several hundred different aluminum alloys exist. Compared to pure aluminum, aluminum alloys are stronger (with strengths sometimes rivaling steel), harder, more durable, and more corrosion resistant. Aluminum alloys are used in a wide range of applications including: automobiles, airplanes, medical equipment, consumer products, wiring, and electronics.
5. Titanium Alloys
Titanium alloys are composed of a titanium base metal and additional elements such as: aluminum, manganese, zirconium, chromium, and cobalt. While pure titanium is already one of the strongest elements, titanium alloys are even stronger. Additionally, titanium alloys are more flexible, and corrosion-resistant. They are often used in aircraft and automotive components, marine applications, and medical devices and equipment.
6. Nickel Alloys
Nickel alloys are composed of a nickel base and other elements such as iron, chromium, and copper. Nickel alloys are stronger, and exhibit desirable magnetic and thermal properties than pure nickel. Nickel alloys are often used in electrical components and electronics.
7. Copper-Nickel Alloys
Copper-nickel (Cu-Ni) alloys are primarily composed of copper and nickel but sometimes include other elements such as silicon, iron, manganese, and zinc to obtain different properties. The properties obtained differ depending on the exact chemical composition of the Cu-Ni alloy. Generally, copper-nickel alloys are excellent electrical conductors, are corrosion resistant, and have high tensile strength (340-650 MPa). Cu-Ni alloys are commonly used in electronics, marine applications, and pipelines.
What Are the Properties of Alloys?
Properties of some of the more common types of alloys are shown in Table 1 below:
Alloy Type | Composition | Properties | Common Uses | Examples |
---|---|---|---|---|
Alloy Type Steel | Composition
| Properties Strong, hard, durable, malleable, machinable | Common Uses Construction, manufacturing, automotive, medical | Examples Structural components in buildings, automotive parts, medical instruments |
Alloy Type Brass | Composition
| Properties Durable, electrically conductive, corrosion resistant, machinable | Common Uses Apparel, hardware, ammunition, marine | Examples Zippers, bolts, fitting, jewelry, musical instruments |
Alloy Type Bronze | Composition
| Properties Strong, hard, corrosion resistant, machinable | Common Uses Artwork, gears, bushings, tools | Examples Sculptures, electrical connectors |
Alloy Type Aluminum Alloys | Composition
| Properties Light, strong, durable, corrosion resistant, machinable | Common Uses Frames for airplanes, automobiles, machinery, etc. | Examples Fuselage for airplanes, bicycle frame |
Alloy Type Titanium Alloys | Composition
| Properties Light, strong, hard, durable, corrosion resistant, biocompatible | Common Uses Medical implants, aircraft, automobiles | Examples Joint implants, airplane parts, automotive parts |
Alloy Type Nickel Alloys | Composition
| Properties Excellent electrical and thermal conductivity, corrosion resistant | Common Uses Electrical and electronic applications | Examples Electrical wiring, transformers, memory storage devices |
Alloy Type Copper-Nickel Alloys | Composition
| Properties Strong, corrosion resistant, ductile | Common Uses Marine applications, power generation, oil and gas piping systems | Examples Offshore oil and gas platforms, boat hulls |
Alloy Type | Density (g/cm3) | Melting Point (°C) | Thermal Conductivity (W/m*K) | Electrical Conductivity (% IACS) |
---|---|---|---|---|
Alloy Type Steel | Density (g/cm3) 7.80-8.00 | Melting Point (°C) 1300-1540 | Thermal Conductivity (W/m*K) 44.0-52.0 | Electrical Conductivity (% IACS) 3-15 |
Alloy Type Brass | Density (g/cm3) 8.40-8.73 | Melting Point (°C) 900-930 | Thermal Conductivity (W/m*K) 111-120 | Electrical Conductivity (% IACS) 28 |
Alloy Type Bronze | Density (g/cm3) 7.40-8.92 | Melting Point (°C) 950-1025 | Thermal Conductivity (W/m*K) 26-83 | Electrical Conductivity (% IACS) 15 |
Alloy Type Aluminum Alloys | Density (g/cm3) 2.50-2.83 | Melting Point (°C) 463-1038 | Thermal Conductivity (W/m*K) 70-237 | Electrical Conductivity (% IACS) 61 |
Alloy Type Titanium Alloys | Density (g/cm3) 4.42-4.84 | Melting Point (°C) 1538-1704 | Thermal Conductivity (W/m*K) 7.2-22.7 | Electrical Conductivity (% IACS) 0.96-1.87 |
Alloy Type Nickel Alloys | Density (g/cm3) 8.09-8.91 | Melting Point (°C) 875-2732 | Thermal Conductivity (W/m*K) 8-17 | Electrical Conductivity (% IACS) 1.35-20.28 |
Alloy Type Copper-Nickel Alloys | Density (g/cm3) 8.91-8.94 | Melting Point (°C) 1170-1240 | Thermal Conductivity (W/m*K) 25-40 | Electrical Conductivity (% IACS) 3.45-9.07 |
Table Credit: https://www.copper.org/
Alloy Type | Corrosion Resistance | Oxidation Resistance | Reactivity | Magnetic Properties | Flammability |
---|---|---|---|---|---|
Alloy Type Steel | Corrosion Resistance Susceptible to corrosion unless surface treated or stainless alloy | Oxidation Resistance Readily reacts with oxygen | Reactivity Reactive to acids and alkalis | Magnetic Properties Ferromagnetic (except austenitic stainless steels) | Flammability Non- flammable |
Alloy Type Brass | Corrosion Resistance Corrosion resistant | Oxidation Resistance Readily reacts with oxygen | Reactivity Reactive to acids and alkalis | Magnetic Properties Non-magnetic | Flammability Non- flammable |
Alloy Type Bronze | Corrosion Resistance Corrosion resistant | Oxidation Resistance Readily reacts with oxygen | Reactivity Reactive to acids and alkalis | Magnetic Properties Non-magnetic | Flammability Non- flammable |
Alloy Type Aluminum Alloys | Corrosion Resistance Corrosion resistant | Oxidation Resistance Readily reacts with oxygen | Reactivity Reactive to acids and alkalis | Magnetic Properties Non-magnetic | Flammability Non- flammable |
Alloy Type Titanium Alloys | Corrosion Resistance Corrosion resistant | Oxidation Resistance Readily reacts with oxygen | Reactivity Reactive to acids and halogens | Magnetic Properties Non-magnetic | Flammability Flammable |
Alloy Type Nickel Alloys | Corrosion Resistance Corrosion resistant | Oxidation Resistance Readily reacts with oxygen | Reactivity Reactive to acids | Magnetic Properties Ferromagnetic | Flammability Non- flammable |
Alloy Type Copper-Nickel Alloys | Corrosion Resistance Corrosion resistant | Oxidation Resistance Readily reacts with oxygen | Reactivity Reactive to acids and alkali | Magnetic Properties Ferromagnetic | Flammability Non- flammable |
Table Credit: https://www.copper.org/
What Are the Applications of Alloys?
Some typical applications of the common alloy groups are listed below:
1. Construction
Steel and aluminum alloys are widely used in construction for their strength and durability. They are used in structural components, roofing, siding, and other building materials.
2. Transportation
Aluminum alloys are perhaps the most widely used type of alloy in the transportation industry. They are lightweight, have a high strength-to-weight ratio, are corrosion-resistant, and are recyclable. Aluminum helps improve fuel efficiency and reduce overall vehicle weight while still fulfilling strength requirements.
3. Electronics
Copper-nickel alloys are used in electrical wiring and connectors for their high conductivity and low resistance. They are also used in batteries, relays, solder frames, and other electrical components.
4. Medical Devices
Stainless steel and titanium alloys are used in medical devices such as implants, prosthetics, and surgical instruments. These alloys are often used in these applications because they are strong, corrosion-resistant, and biocompatible.
5. Jewelry
Bronze, copper-nickel, nickel-silver, aluminum, and many more alloys are used to create jewelry. Alloys are often used in jewelry because they are easier to form and are more durable than pure metals. Additionally, different colors can be obtained with alloys that would not be possible with pure metals.
6. Manufacturing
Alloys of all kinds are used in manufacturing to fabricate parts for the automotive, aerospace, construction and heavy equipment, medical, consumer product industries, and more. Steel, brass, aluminum, and titanium alloys are all often used in manufacturing for machining, casting, or forming. Alloys are used in manufacturing because they are much easier to work and form than pure metals.
7. Art and Sculpture
Alloys such as bronze and brass are widely used in artwork and sculpture for their unique colors, durability, and workability.
What Are the Benefits of Alloys?
Some of the benefits of using alloys instead of pure metals are listed below:
- Better Strength: Alloys are stronger than pure metals because adding other atoms into the lattice structure of the base metal deforms the lattice just enough to make it more difficult for the atoms to move around.
- More Versatility: Alloys are more versatile than pure metals because they have desirable properties that are not present in pure metals. Alloys are generally stronger, harder, and more corrosion-resistant.
- Increased Hardness: Alloys are harder than pure metals for the same reason that they are stronger than pure metals. Additional atoms strain the lattice structure of the base metal and make it more difficult for atoms to dislocate.
- Can Have Increased Corrosion Resistance: Alloys can be more corrosion-resistant than pure metals depending on the additional alloying elements and how they interact with the surrounding environment. Some alloying elements, such as zinc, chromium, and nickel, readily react with oxygen and form protective layers on alloy surfaces. This barrier prevents oxygen from penetrating the material and causing it to corrode.
- More Cost Effective: Alloys are more cost-effective than pure metals because the processes to make alloys are generally cheaper than the processes to refine pure metals.
What Are the Limitations of Alloys?
The limitations of alloys compared to pure metals are listed below:
- Less Ductile: Alloys are less ductile than pure metals because of the addition of extra atoms to the lattice structure of the base metal and the consequent reduction in the number of slip systems available for plastic deformation.
- Difficult to Weld: Alloys have lower melting points than their pure metal counterparts. This makes alloys harder to weld.
- Difficulty in Recycling: Alloys are more difficult to recycle than pure metals because alloys have many constituent materials.
- Can Be More Prone to Corrosion: Some alloys are more susceptible to different forms of corrosion than pure metals
- Environmental Concerns: The production of some alloys can release hazardous and harmful fumes into the atmosphere.
Are Alloys Rust-Proof?
Mostly yes. Alloys that do not contain iron will not rust, since rust is specifically iron oxide. However, alloys that do contain iron will eventually rust, except for the stainless steel.
Are Alloys Hypoallergenic?
Mostly yes. Alloys that do not contain nickel, cobalt, and chromium (the metals that usually cause allergies) are hypoallergenic. If allergic, avoid using alloys with these metals.
Are Alloys Metals?
Yes, alloys are metals. They are good conductors of heat and electricity and have shiny surfaces. For more information, see our guide on Metalloids.
What Is the Difference Between an Alloy and a Metal?
An alloy is a material consisting of base metal and additional elements. A “metal” is a classification for ductile materials, that have a lustrous appearance, and are excellent electrical and thermal conductors as compared to other classes of materials. All alloys are metals, but not all metals are alloys.
What Is the Difference Between an Alloy and Aluminum?
An alloy is a material composed of base metal and additional elements. Aluminum is a pure metal that is not combined with other elements. However, many aluminum alloys have been developed to have desirable properties that otherwise do not exist in pure aluminum.
Summary
This article presented alloys, explained what they are, and discussed the various types and their properties. To learn more about alloys, contact a Xometry representative.
Xometry provides a wide range of manufacturing capabilities and other value-added services for all of your prototyping and production needs. Visit our website to learn more or to request a free, no-obligation quote.
Disclaimer
The content appearing on this webpage is for informational purposes only. Xometry makes no representation or warranty of any kind, be it expressed or implied, as to the accuracy, completeness, or validity of the information. Any performance parameters, geometric tolerances, specific design features, quality and types of materials, or processes should not be inferred to represent what will be delivered by third-party suppliers or manufacturers through Xometry’s network. Buyers seeking quotes for parts are responsible for defining the specific requirements for those parts. Please refer to our terms and conditions for more information.
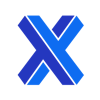